Zatímco při klasické výrobě leteckých motorů může trvat devět až dvanáct měsíců, než držíte v ruce první součástku, v případě 3D tisku jsou to po zhotovení designového návrhu řádově dny, maximálně týdny. Výrobce leteckých motorů GE Aviation Czech takto při výrobě prvního prototypu nového motoru Catalyst, určeného pro malá korporátní letadla, ušetřil téměř rok.
„Technologie 3D tisku nám umožnila vyvíjet a následně vyrábět mnohem komplexnější tvary. Z padesáti dílů, které bychom například v případě odlévání tvořili zvlášť, zvládneme vytisknout celek. Namísto téměř 2800 součástek jich nyní motor obsahuje pouze necelé dva tisíce. Oněch 855 dílů bylo nahrazeno 12 vyrobenými aditivní technologií,“ říká šéf společnosti Milan Šlapák.
HN: Co je na novém motoru speciálního?
Kromě toho, že je ze třetiny vyroben pomocí 3D tisku, jde o první motor v kategorii obchodního letectví, což jsou menší letadla nebo soukromé tryskáče, který je plně digitální. Motor i vrtule jsou řízeny počítačem, který v průběhu chodu vyhodnocuje jejich chování, sleduje, v jaké fázi letu se nachází, a sám rozhoduje, jak motor mění své chování na základě vnějších a vnitřních podmínek. Nic takového dnes v tomto segmentu v provozu neexistuje. Digitalizace motoru snižuje pracovní zátěž pilota, který se tak může plně věnovat letu a soustředit se, co se děje vně letadla, nikoliv v kokpitu. Tímto motor sekundárně zvyšuje bezpečnost letového provozu. Nehledě na to, že když motor sám sebe optimalizuje, optimalizuje i výkon a spotřebu paliva.
HN: Ve velkých leteckých motorech je ale tato technologie známá. Nelze ji tedy jednoduše přenést na menší motor?
Takto jednoduché to není. Pokud bychom vzali úplně stejný motor, jaký je v Airbusu 320, a rozhodli se ho zmenšit třeba jedna ku dvaceti, technologie promítnuté do konkrétního tvaru dílů nemusí fungovat stejně. Musí projít změnou. V menších velikostech na sebe termodynamické zákony působí jinak.
HN: Využívá se v letectví umělá inteligence?
V tuto chvíli ne. Pravidlo číslo jedna v letectví je bezpečnost. Létá se vysoko a rychle. Než úřady pustí do vzduchu nový produkt, musí výrobce prokázat, že vše, co se v něm odehrává, je predikovatelné a bezpečné. Pokud bychom do leteckého výrobku zabudovali umělou inteligenci pro jeho řízení, popřípadě strojové učení, nedokážeme v současné době zmapovat rozhodovací procesy umělé inteligence. Vidíme sice výsledky rozhodování umělé inteligence a dokážeme posoudit, zda se rozhodla správně, nebo ne, nicméně nevíme, jak se k danému rozhodnutí dopracovala a proč. To, že digitální řízení motoru je chytré a bezpečné, je zajištěno naprogramovaným softwarem. Proto přesně víme, jak budou probíhat rozhodovací procesy řízení. U umělé inteligence to dnes neví nikdo.
HN: Vraťme se k 3D tisku. Jaké materiály používáte?
Motor tiskneme pouze z kovu, respektive kovových slitin. Použili jsme plast ve chvíli, kdy inženýři ještě finalizovali design jednotlivých komponent a modulů motoru. A zde jsme také výrazně ušetřili čas. Poskládali jsme celý motor z plastových součástek a zkoušeli jsme, jak bude fungovat montáž, ještě dříve, než vznikly první prototypové části. Podobně jako si děti hrají s legem. Pak bylo jednodušší vyhodnotit, který díl by si zasloužil vylepšit design či který prostor pro montáž více zpřístupnit. Ještě nikdo v letectví nespustil funkční prototyp nového motoru na zkušebně za dva roky.
HN: V případě kovových částí bývá problém s povrchem. Procházejí jednotlivé díly ještě další úpravou?
V leteckém průmyslu jsou extrémně nízké rozměrové tolerance. Požadavek na přesnost je v porovnání s ostatními odvětvími na zcela jiné úrovni. Finální úpravy povrchu provádíme, ale celý proces je mnohem jednodušší, než kdybychom díl obráběli z nového celku. Říká se tomu buy‑to‑fly ratio, poměr nakoupeného objemu prvotního materiálu či polotovaru a objemu, který ve skutečnosti létá. Při obrábění komplikovaných tvarů zůstane z původního kusu v některých případech jen malý podíl. Při 3D tisku jsou zbytky minimální. Poměr objemu vytištěného materiálu a materiálu komponentu, který létá, je téměř 1 : 1.
HN: Jaké další výhody má pro vás 3D tisk?
Jednoznačně časovou úsporu, která jde ruku v ruce s šetřením nákladů. Je rozdíl, když předáme zákazníkovi produkt za měsíc nebo za tři. O co více jsme schopni zkrátit výrobní cyklus, o to dříve obdržíme hotovost od zákazníků. A to je v dnešní době velmi důležitá věc. Další výhodou je simplifikace. Jsme schopni vytisknout celou sestavu nebo podsestavu jako jeden celek namísto montáže několika desítek součástek. Pomocí 3D tisku je možné vytvářet tvary, které jiná technologie nezvládne. I díky tomu mohou být výsledné celky lehčí, přestože mají stejné mechanické vlastnosti jako ty vyrobené klasickou cestou. A v letectví váha přímou úměrou ovlivňuje spotřebu paliva. To je velké plus.
HN: Vytvořili jste samostatnou divizi GE Additive. Proč?
Bylo nám jasné, že 3D tisk zásadním způsobem změní průmysl. A my jsme chtěli být těmi, kteří udávají trendy. Provedli jsme akvizice několika firem, jež z našeho pohledu měly takové technologie, které v budoucnu uspějí, a dále firem, jež mají expertizu v designu dílů pro aditivní výrobu. Znalost, jak navrhovat pro tisk a jak následně tisknout, je vysoce ceněné know‑how.
HN: Co dalšího máte v plánu, aby vám zůstal status firmy, která udává trendy?
Směr, kterým se odvětví ubírá, je schopnost tisknout více dílů najednou, což umožňuje zvětšující se plocha tiskárny i počet paprsků. Sériová výroba ve velkých objemech je nutný předpoklad pro industrializaci aditivní výroby. Zároveň neustále sledujeme, vyvíjíme a certifikujeme nové materiály, obzvláště jejich kombinace. Tak, jak se vyvíjí 3D tisk, pokračuje i vývoj defektoskopie (metody odhalování vad – pozn. red.). Díl sám o sobě je jeden velký svár a tvary uvnitř jsou velmi komplikované. Je potřeba zajistit, že je v pořádku a neobsahuje trhliny nebo mikroporozitu, která by mohla způsobit prosakování paliva či oleje. Používáme technologie jako rentgeny, ultrazvukové inspekce a podobně. Je to také design sám o sobě. Inženýři mají naučené zažité a prověřené tvary, které v návrzích používají. Nyní software a počítačové technologie umožňují navrhnout zcela nový tvar, se kterým se dříve nepracovalo, protože na to nebyla k dispozici výpočtová kapacita. Bez ní by lidský mozek nebo lidská dovednost nedokázaly takový tvar navrhnout.
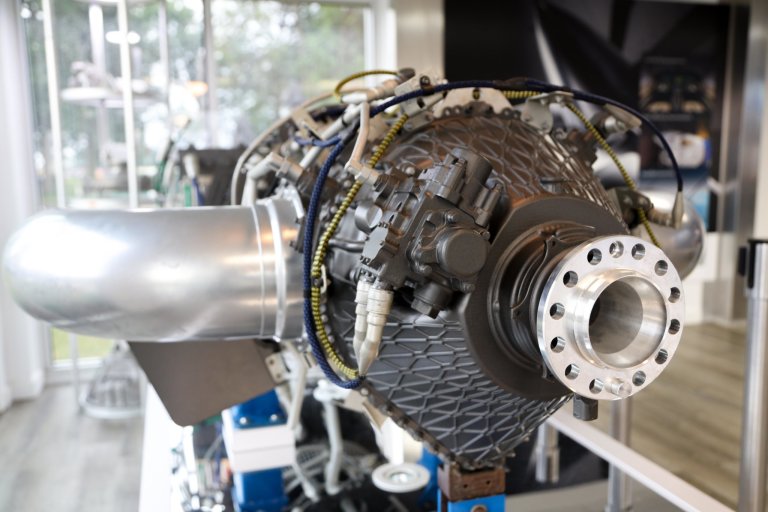
HN: Jak to funguje?
Do softwaru nebo aplikace se v podstatě nadefinuje, jaký je cíl dílu, k čemu se bude využívat a jeho body napojení na zbytek systému nebo produktu. A zároveň programu určíme kritérium optimalizace. Zda upravujeme design pro váhu komponentu či jeho pevnost, pružnost nebo výrobní náklady. Aplikace pak začne navrhovat různé tvary. Tím, že to dělá extrémně rychle, mohou vzniknout tisíce možných designů. Každá možnost je následně vyhodnocena podle zadaného kritéria nebo kritérií. Software po ukončení doporučí tvar, který nejlépe vyhovuje zadaným požadavkům. To by tým lidí nikdy nezvládl v rozumném časovém období a ani v akceptovatelných nákladech na vývoj. Klasickými metodami je možné navrhnout a vyhodnotit řádově jednotky návrhů. Nejzajímavější je, že součástky, které vznikají, jsou úplně jiné, než na které jsme zvyklí. Často se hovoří o alien tvarech nebo alien designu. Tvary jsou opravdu jak odněkud z vesmíru. A to jsou věci, které by lidský mozek jen těžko dokázal v objemech, s nimiž průmysl běžně pracuje.
HN: A taková věc je opravdu více funkční než její předchůdce?
Ano, takto navržený tvar je lépe optimalizován dle zadaného kritéria než tvar navržený klasickými metodami. A to je know‑how, které má pouze omezený počet firem. Tvary jsou na výrobu značně komplikované a právě 3D tisk je dokáže zvládnout.
HN: Kam by se 3D tisk mohl posunout za 10 let?
Těžko říct. Vím ale jistě, že už za pouhé tři roky bude opět o několik generací dál. Vývoj jde vysokou rychlostí dopředu. Každý půlrok se zvětšuje plocha, kterou tiskárna dokáže zvládnout. Jestliže tiskárny na metalický prach začínaly na rozměrech 20 × 20 centimetrů, dnes je to téměř metr na metr. Druhá výhoda je, že tiskárny už netisknou jen jeden kus naráz, ale protože se zvětšuje plocha tiskárny a zvyšuje se výkon paprsku, je možné tisknout více produktů najednou. Myslím, že trend půjde tímto směrem. Díl se navíc může skládat z různých materiálů. Už existují tiskárny, jež je dokážou kombinovat. Takto vytištěný díl má ve svých různých částech odlišné mechanické vlastnosti. Něco může být naprosto pevné a na dalším místě pružné. To otvírá další možnosti pro širší využití aditivní výroby. Dále se vývoj ubírá k tomu, že aditivní výrobu je možné používat i na opravy. Když vytiskneme kovovou součástku, která je mechanicky poškozena, nemůžeme ji slepit jako modelínu. Nyní ale specifické technologie 3D tisku dokážou pomocí paprsku laseru vrátit atomy původního materiálu na místo zasažené mechanickým poškozením a doplnit původní tvar. Využití aditivní výroby jako opravárenské technologie přináší ohromné finanční úspory pro uživatele.
Článek byl publikován ve speciální příloze HN Strojírenský veletrh.
Přidejte si Hospodářské noviny
mezi své oblíbené tituly
na Google zprávách.
Tento článek máteje zdarma. Když si předplatíte HN, budete moci číst všechny naše články nejen na vašem aktuálním připojení. Vaše předplatné brzy skončí. Předplaťte si HN a můžete i nadále číst všechny naše články. Nyní první 2 měsíce jen za 40 Kč.
- Veškerý obsah HN.cz
- Možnost kdykoliv zrušit
- Odemykejte obsah pro přátele
- Ukládejte si články na později
- Všechny články v audioverzi + playlist