Kolem 70 programátorů a projektantů se v ostravských hutích ArcelorMittal pod vedením ředitele Miroslava Hýbla stará o automatizaci a digitalizaci výroby oceli. Jde o necelé jedno procento z více než sedmi tisíc zaměstnanců hutí. Divize, kterou ArcelorMittal Ostrava založil v roce 2015, sídlí v nevelké budově areálu hutí. Tomu dominují vysoké pece, koksárenské baterie, ocelárna nebo 54 metrů vysoký fluidní kotel pro výrobu páry, z jehož střechy je vidět, jak obrovské hutě v Ostravě vlastně jsou.
Přesto může právě tato malá skupina lidí v příštích letech zásadně proměnit fungování největších českých oceláren. To nezmění ani nedávno ohlášený záměr managementu ArcelorMittalu ostravský podnik prodat. Světová ocelářská jednička hodlá koupit italské hutě Ilva v Tarentu, které jsou největší v Evropě, a bude se muset některých jiných provozů zbavit, aby k tomu získala souhlas Evropské komise.
Ostravský ArcelorMittal už od obnovení divize, kterou v minulosti zrušil, do automatizace investoval přes 200 milionů korun. Další stamiliony ještě podnik v příštích letech čekají. Zlomové budou hlavně výsledky projektu, který v podniku začal letos v březnu a který mapuje všechny výrobní procesy v huti.
Ocel 4.0. Největší hutě v Česku investují do digitalizace
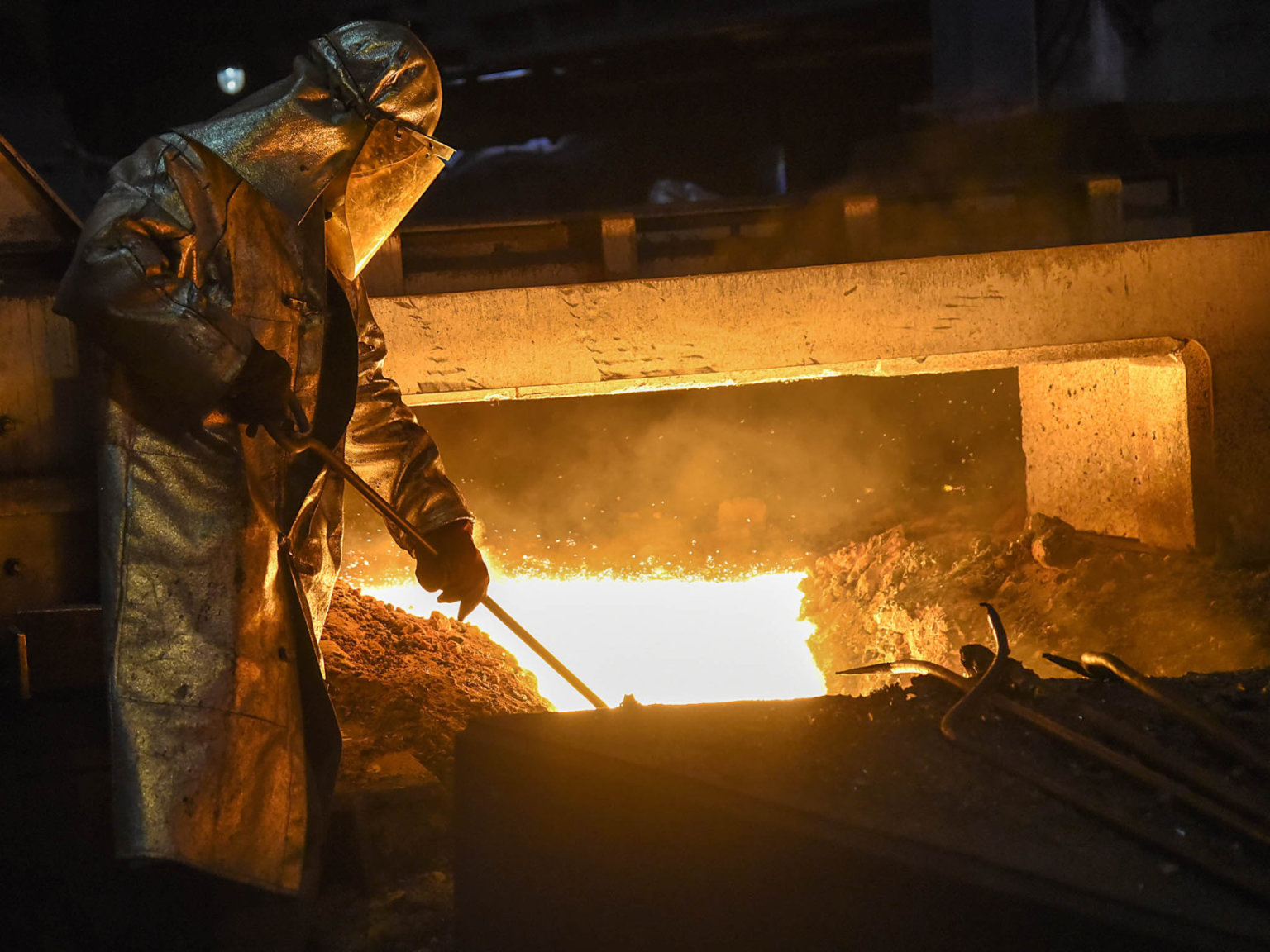
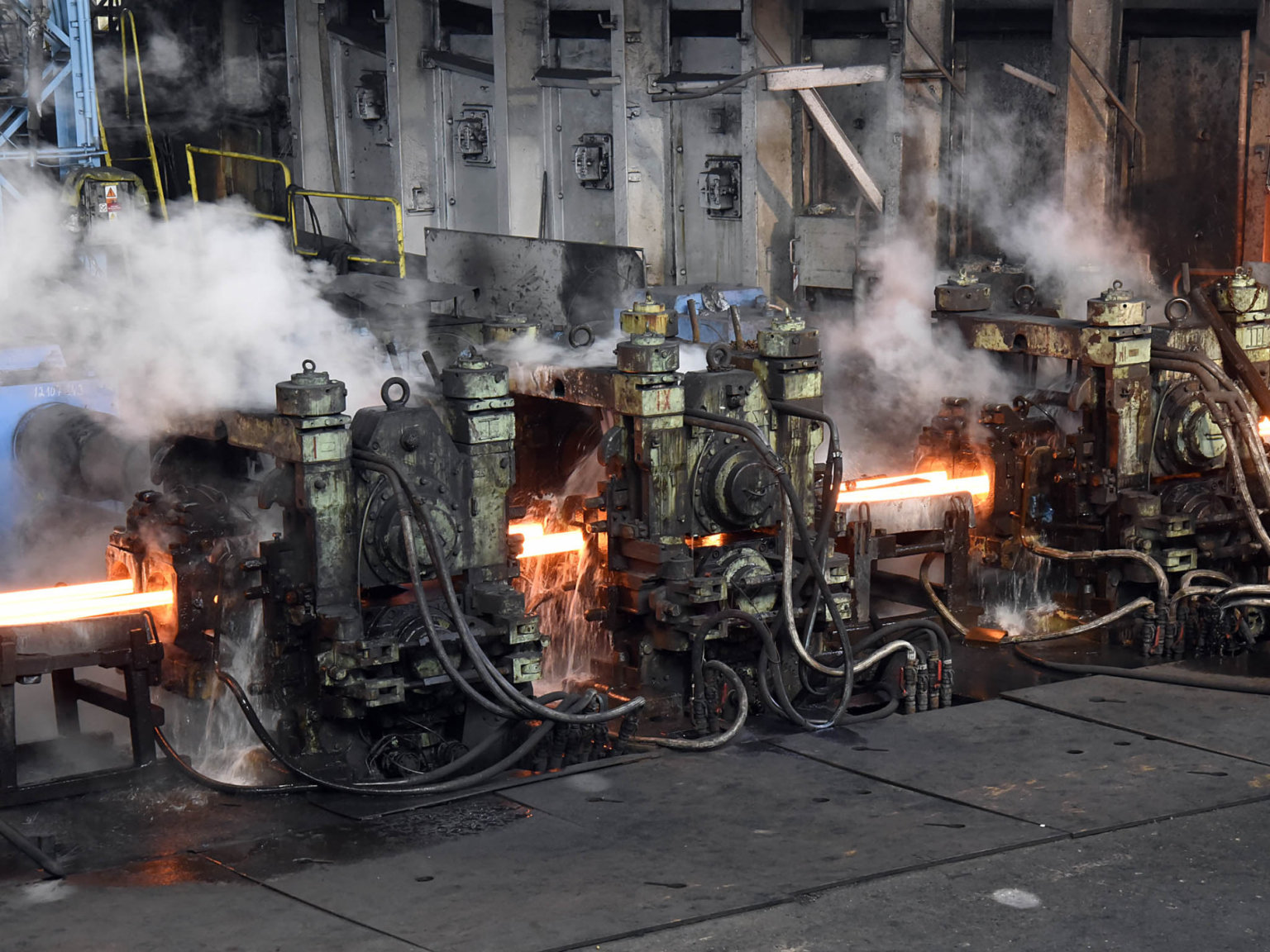
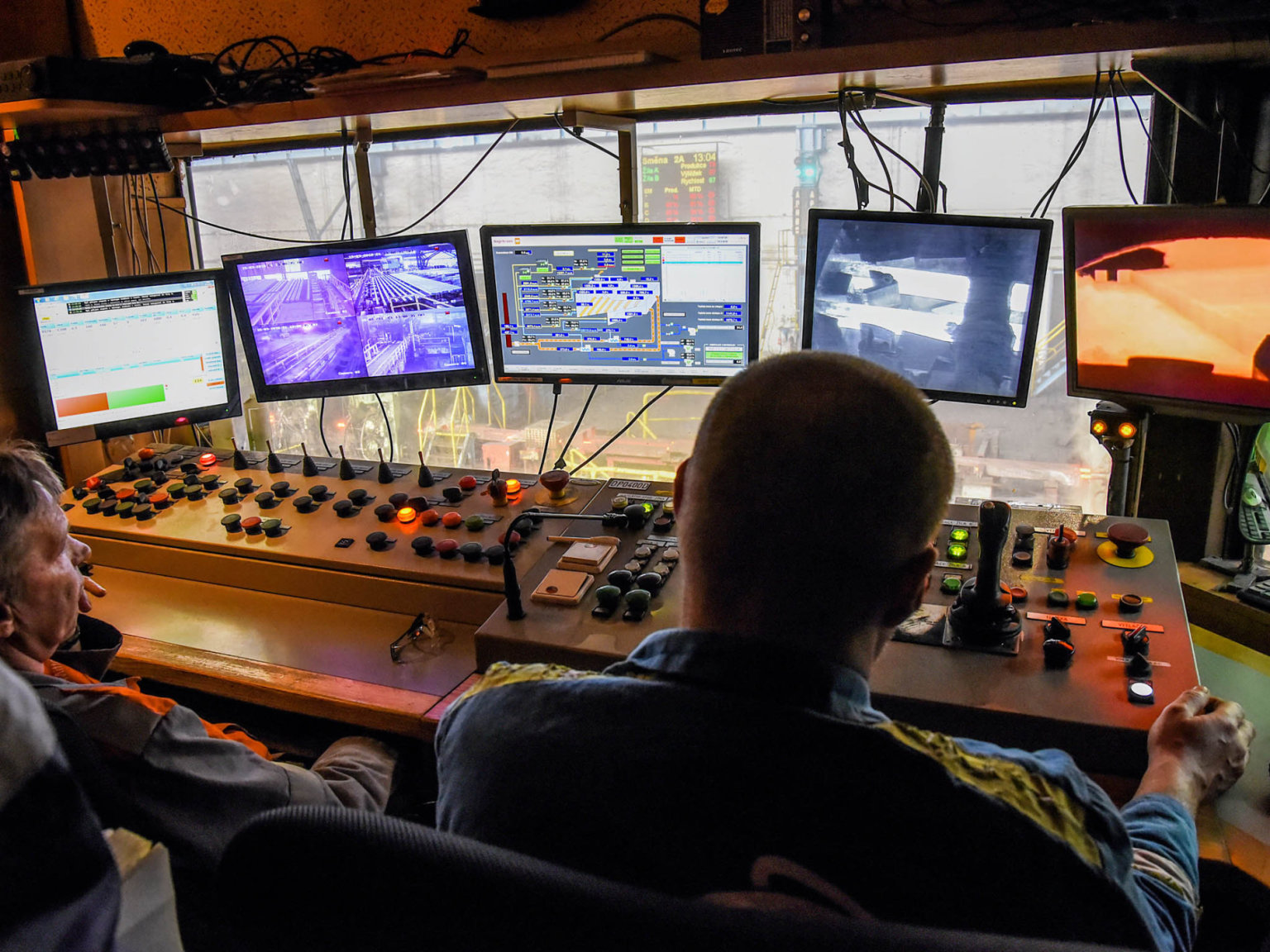
"Změříme nejen, co každý zaměstnanec v jednotlivých krocích dělá, ale hlavně to, jaké informace se v procesu vytváří, kde se uchovávají a jak se s nimi pracuje. Hotové to bude do roku 2020," řekl Hýbl. Podle něj však zavádění Průmyslu 4.0 v ocelárnách neznamená, že ocel začnou v budoucnu vyrábět roboti. "Lidská práce je v řadě činností nenahraditelná, protože je tam nejefektivnější. Výroba oceli se navíc nepodobá nejvíce automatizované sériové výrobě v automobilkách, protože se v ocelářství pracuje s hmotou o tisíci a více stupních Celsia a hmotnostmi stovek tun, což vyžaduje odlišný přístup k robotizaci," uvedl Hýbl s tím, že nynější roboti toto nezvládnou.
Model pro vysokou pec
Největší prostor pro Průmysl 4.0 v hutích je ale podle Miroslava Hýbla ve vytváření "digitálních dvojčat", která propojují reálně existující zařízení či stroj s jeho kopií v kybernetickém prostoru. V Ostravě takto funguje virtuální model na jedné ze dvou funkčních vysokých pecí, kde se z připraveného aglomerátu ze železné rudy, koksu a strusky vytváří při teplotě 1500 stupňů surové železo. To je základem pro výrobu ocelových polotovarů (tyčovitých sochorů a obdélníkových bran) i následných výrobků z válcoven nebo drátoven.
Ve vysokých pecích řídí provoz na směně dva operátoři ve velíně a mají k dispozici údaje ze senzorů a kamer, které sledují kolem pěti tisíc položek − od teploty, tlaku, složení suroviny dodávané do pece (vsázka) až po složení hotového surového železa. To z pece vytéká přibližně každé tři hodiny při odpichu, jak se vypuštění stovek tun žhnoucí žlutavé hmoty odborně nazývá.
Speciální software operátorům usnadňuje práci, protože predikuje nejlepší postup, aby při výrobě nedošlo k žádným výkyvům. "Základem fungování vysoké pece je rovnoměrnost, jakýkoli větší výkyv je nežádoucí," řekl Hýbl.
Vysoká pec ArcelorMittalu v Ostravě běží nepřetržitě 24 hodin už po dobu 10 let a ročně vytaví asi dva miliony tun surového železa. Jakékoli zastavení pece by znamenalo stamilionové ztráty. Predikce dění uvnitř vysoké pece, kde se taví surové železo, je zatím jediná možná, protože žádné čidlo by teplotu uvnitř pece nevydrželo. Díky modelu se ušetří i energie a koks, který během zpracování drží rudu ve středu vysoké pece a je potřeba pro proces takzvané redukce, kdy se uvolňuje surové železo. Na výrobu jedné tuny železa je potřeba přibližně 600 kilogramů koksu.
Koksárny se týkal i jeden z prvních větších projektů Hýblova týmu, kdy v roce 2017 lidskou posádku lokomotivy a vozů pro přepravu koksu k jeho uhašení nahradily automatem řízené stroje. Tím se na jednu směnu ušetřila práce šesti lidí. Automatizovaná je i přeprava surového železa z vysoké pece do ocelárny.
Automatická ruka
Nový projekt, který po pilotní fázi funguje naplno od letošního března, se týká přímo závěrečné fáze ocelářské produkce, konkrétně výroby válcovaných drátů. Ty se vyrábí ze sochorů dlouhých přes 11 metrů, které váží 1250 kilogramů. Z pece je dosud do zhruba 200 metrů dlouhé výrobní linky vkládali lidé. Fyzicky náročná práce nebyla tak efektivní jako nynější systém, kdy sochory vytlačuje automatická tyč. Nový systém funguje pomocí infračervené kamery a speciálně vyvinutého softwaru, který dokáže najít pozici sochoru v peci a navést výtlačnou tyč na správné místo. Umí reagovat na měnící se podmínky v peci. Díky tomu se tak sochory vytlačují každou minutu a rozestupy mezi nimi nejsou delší než pět sekund, což je tempo, které člověk nemůže zvládnout. I díky tomu vypadá rozlehlá drátovna vlastně docela opuštěně.
Logistika 4.0
Vůbec největší prostor pro nové postupy ale vidí Miroslav Hýbl z ArcelorMittalu u logistiky. Jeho vzorem je koncernový závod v belgickém Gentu, kde se vyrábí ocelové svitky. Celá logistika po jejich dokončení tam probíhá automaticky, když si řídicí systém samostatně zvolí místo k uložení vyrobeného svitku ve skladu a pošle pro něj jeřáb, který svitek automaticky uloží.
V Ostravě už čtvrt roku funguje automatický vážní systém pro kamiony, které odvážejí skoro polovinu vyrobené produkce hutí. Pomocí systému se monitoruje a koordinuje pohyb kamionů v areálu firmy. Řidič kamionu si v samoobslužném registračním místě vyzvedne kartu a vytiskne všechny potřebné dokumenty. S kartou se může pohybovat po celém závodě. Šetří se tím čas skladníků i řidičů, kteří by jinak museli několikrát vystupovat z auta. Teď jim stačí najet na váhu a po přiložení karty se jim všechny dokumenty vytisknou.
"Ideál je, aby řidič od vjezdu přes odebrání zboží po výjezd přišel do minimálního kontaktu s našimi zaměstnanci, hlavně při nakládce zboží," řekl Hýbl.
ArcelorMittal zavádí prvky automatizace a digitalizace i ve svých dalších závodech. Třeba model u vysoké pece v Ostravě se používá ve všech závodech koncernu, kde se najednou sdílí data v reálném čase. Centrum, kde se globální data shromažďují, je ve Francii. Podobně jako ArcelorMittal zavádí Průmysl 4.0 v ocelářství i další významné hutě, včetně Třineckých železáren, které jsou druhým podnikem v Česku, který provozuje celý výrobní cyklus od vysoké pece po výrobu drátů a plechů.
K digitalizaci a automatizaci zároveň tlačí ocelářství v Evropě i dva spolu nesouvisející trendy. Konkurence levnější mimoevropské oceli zvyšuje tlak na úsporu nákladů. A modernizace výroby je vhodnou odpovědí − i proto, že Čína, kde se vyrábí největší množství oceli na světě, se zavádění nových technologií také nebrání. Skandál kolem japonských oceláren Kobe Steel, jež několik let falšovaly certifikáty kvality u tisíce tun svých výrobků (byť hlavně u produkce z hliníku a mědi), pak zároveň vytváří u odběratelů z řad průmyslu tlak na digitalizaci, protože je díky ní možné dohledat historii každého jednotlivého výrobku.
Ocel 4.0. Největší hutě v Česku investují do digitalizace
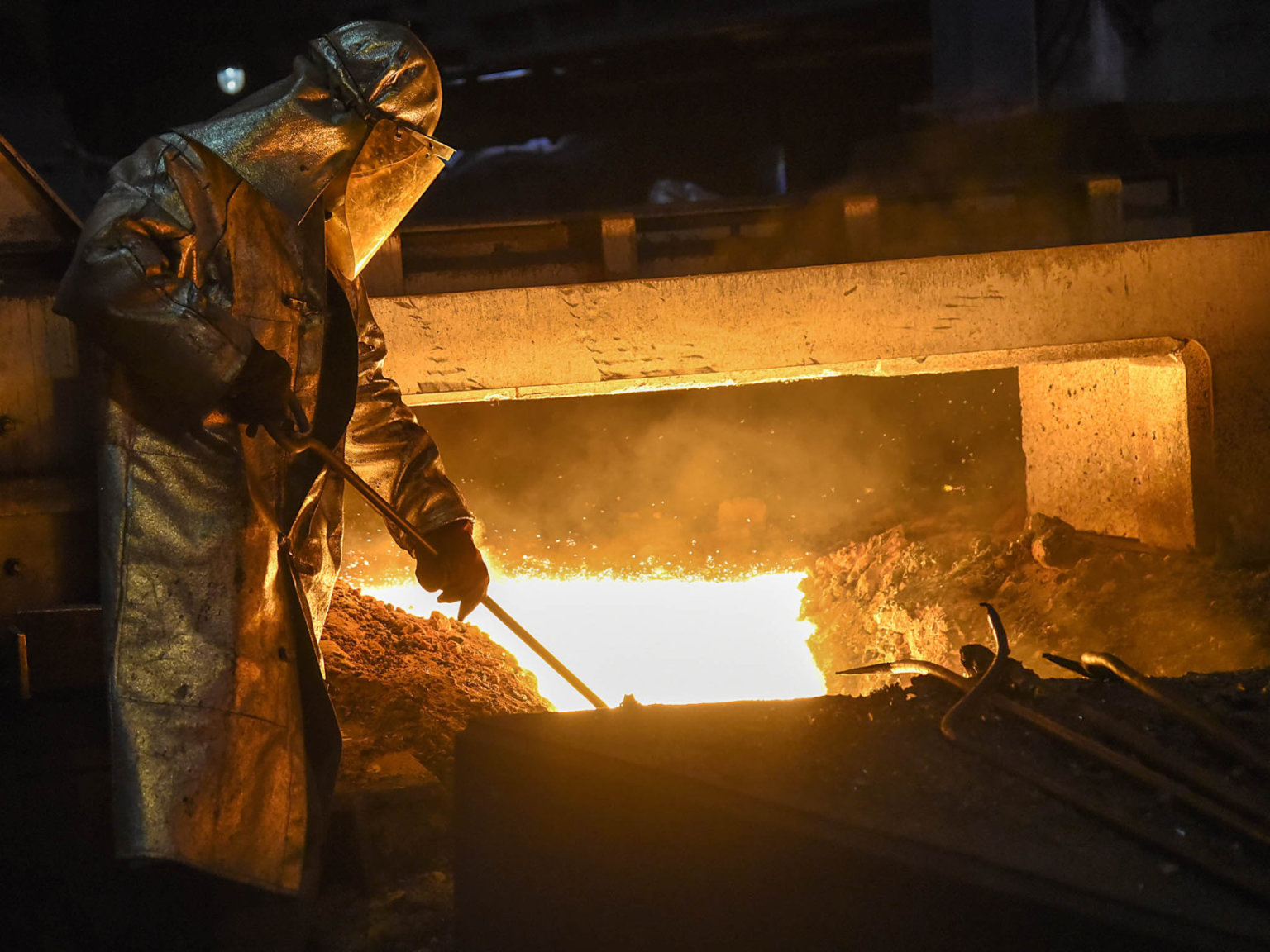
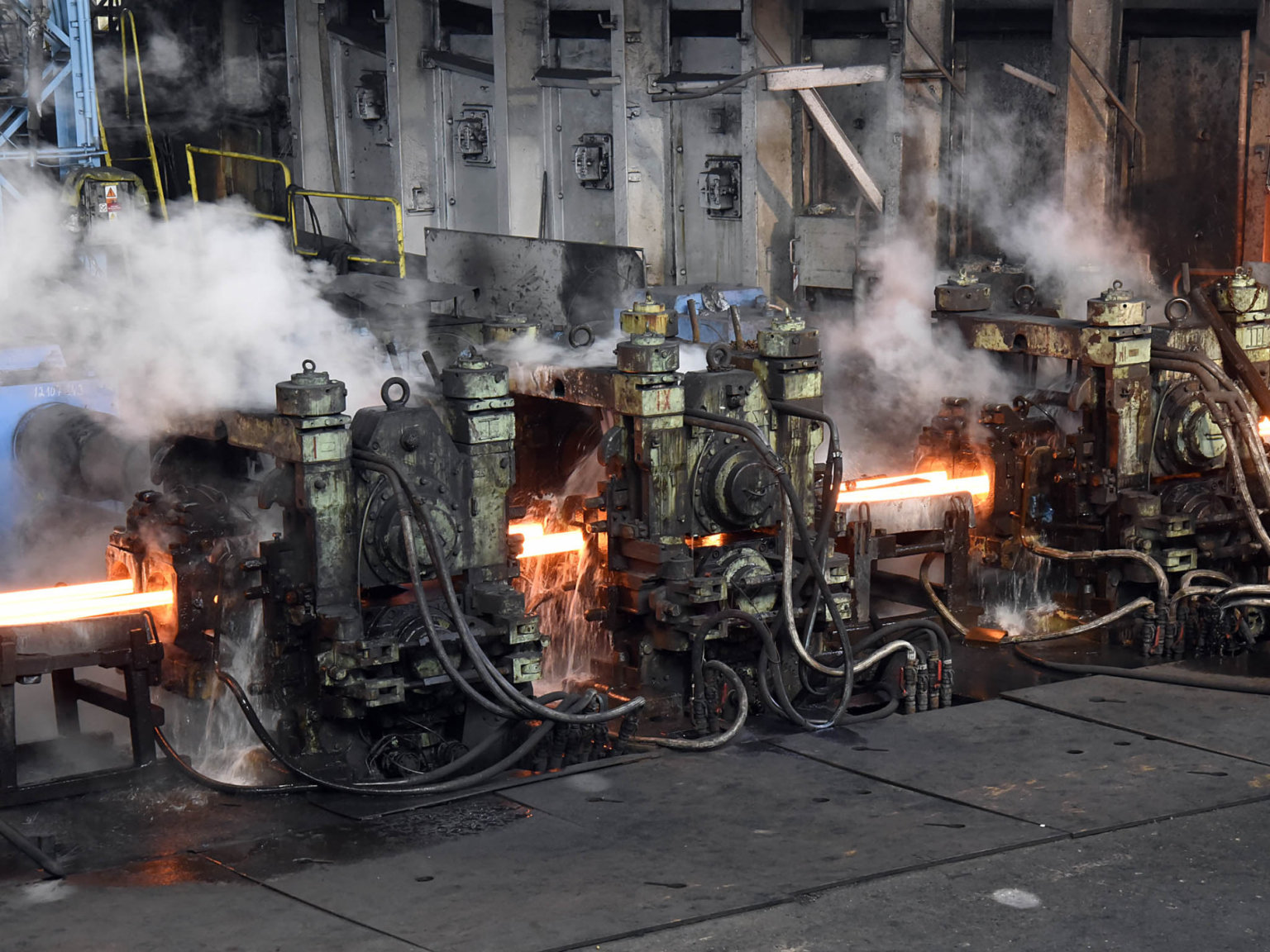
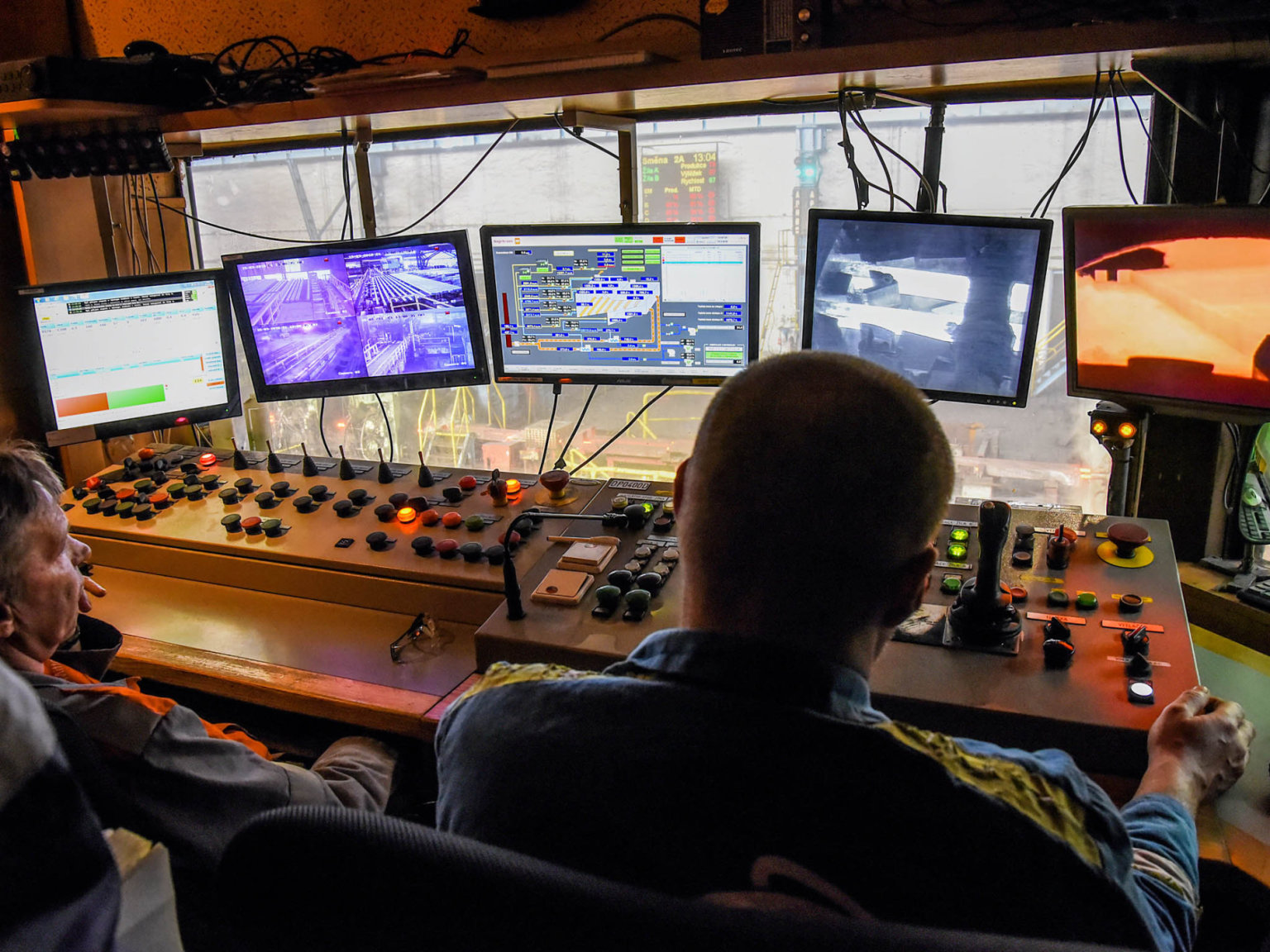
Přidejte si Hospodářské noviny
mezi své oblíbené tituly
na Google zprávách.
Tento článek máteje zdarma. Když si předplatíte HN, budete moci číst všechny naše články nejen na vašem aktuálním připojení. Vaše předplatné brzy skončí. Předplaťte si HN a můžete i nadále číst všechny naše články. Nyní první 2 měsíce jen za 40 Kč.
- Veškerý obsah HN.cz
- Možnost kdykoliv zrušit
- Odemykejte obsah pro přátele
- Ukládejte si články na později
- Všechny články v audioverzi + playlist