Stroje s námi mluví. Prostřednictvím dat nám říkají, jak mohou být výkonnější, jak mohou mít delší životnost, kde dělají chyby, kdy si potřebují dát na chvíli pauzu a trochu promáznout šroubky, kdy a proč se přehřívají, a také nám řeknou, že tamten vstřikovač na druhém konci haly brzo dostříká, a jestli nechceme, aby se zastavila výroba plastů, měli bychom co nejrychleji objednat náhradní díly.
Společnost Accenture se například v Rumunsku nedávno podílela na vybudování moderní továrny pro výrobce praček, ledniček a kuchyňských spotřebičů. „Pomáhali jsme při implementaci nového systému řízení výroby (MES) na bázi technologie SAP. Vytvořili jsme technologickou vrstvu, která pomocí konceptu IoT (Internet of Things, síť fyzických zařízení vybavených elektronikou, která jim umožňuje vyměňovat si data – pozn. red.) integruje data ze strojů a technologií s daty podnikového informačního systému, jež se týkají zakázek, plánování výroby, řízení skladu a podobně. Navrhli jsme také snadno použitelné ovládací panely pro zobrazení dat téměř v reálném čase. Celkem šlo o integraci více než 250 strojů a 14 různých IT systémů,“ říká Pavel Vrba, který se v Accenture věnuje oblasti digitalizace výroby.
Většina pracovníků používá tablet připojený k firemnímu intranetu a novému výrobnímu systému a může v reálném čase konzultovat pracovní příkazy a pokyny. „Pokud například dříve vedoucí výroby několikrát denně žádal vedoucího výrobní směny o aktualizace stavu výroby, může nyní sám kontrolovat aktualizace v reálném čase na svém notebooku nebo tabletu,“ uvádí Vrba přínosy projektu.
Další konkrétní příklad z rumunské továrny ukazuje zjednodušení práce operátora výroby, jehož úkolem je připojit motor ke každé pračce. Dříve mu motory na pracovní stůl přivážel vysokozdvižný vozík a byly naskládané v krabicích. Operátor si musel zavolat kolegu, aby mu pomohl těžké krabice zvednout a přenést je na jeho pracovní stůl. „Nyní si může pomocí tabletu vyžádat doručení přesně na konkrétní čas, a to prostřednictvím systému autonomních vozidel, která mu doručí krabice s motory až na stůl. Tím se eliminuje i zdravotní riziko a operátor může rychleji odvést kvalitnější práci,“ dodává Pavel Vrba, podle kterého nové řešení pomohlo firmě automatizovat až 80 procent výrobních procesů a snížit provozní náklady o 11 procent.
Velké množství dat, která firmy pro efektivní řízení potřebují, již v nějaké formě sbírají a ukládají. Typicky u nových strojů a výrobních linek, které jsou na to připraveny. Ne vždy jsou ale data plnohodnotně využita. „Za prvé jsou oddělena v takzvaných silech, tedy v různých navzájem nepropojených systémech či databázích. Za druhé jsou v syrovém stavu, bez kontextu, v obrovských kvantech,“ popisuje problémy Pavel Vrba.
Oba faktory pak způsobují, že je těžké se v datech vyznat a vytěžit z nich nějaké hodnotné informace. „Cestou ke zlepšení je použití cloudových technologií, kde je snazší data z jednotlivých zdrojů agregovat a pomocí nástrojů typu business intelligence jednoduše analyzovat a zobrazovat,“ vysvětluje.
Dynamický autoprůmysl
Sbírání a efektivní využívání dat pak ovlivňuje dynamičnost oboru. Ve strojírenství je to patrné zvláště v automobilovém průmyslu. Přicházejí nové modely aut, stávající se neustále vylepšují a s tím se mění i výrobní technologie. „U zpracování surovin je to jiné. Postavíte pivovar nebo mlékárnu, deset patnáct let vám budou v klidu sloužit a data, která nasbíráte, můžete použít pro závod, který postavíte jinde. U unikátních technologií, kde se produkt mění dynamicky, jako je automotive, je využívání dat mnohem složitější,“ říká Jan Václavovič, obchodní ředitel JHV Group, jejíž výrobní linky a robotická pracoviště lze najít v mnoha zemích světa.
Dynamickým vývojem například procházejí svařovny ve Škodě Auto, kde je nyní nasazeno přibližně 3500 průmyslových robotů obsahujících miliony řádků instrukcí a další miliony parametrů. „Každý den dochází ke změnám, ať už při nové výstavbě, nebo při kontrole kvality stávající výroby. Jakákoliv manuální správa robotických programů by byla nemožná a neefektivní. Používáme proto softwarové nástroje, které nám pomáhají v orientaci v tomto rozsáhlém prostředí svařovny,“ říká Jan Čejka, projektový koordinátor robotizace svařoven ve Škodě Auto.
„Osobně to nazývám softwarovým pozorovatelem, protože monitorujeme aktuální stav. Základním zdrojem informací je v tomto případě robotická záloha. Ze záloh jsme schopni vytěžit přehled o aktuálním stavu svařovny. Zajímají nás základní informace o robotu, verze aplikačních balíků, ale i stav jednotlivých programů. V případě i sebemenší chyby v robotickém programu jsme schopni velice rychle připravit kontrolní rutinu a provést plošný sken svařovny. U dotčených robotů pak můžeme zorganizovat nápravu,“ vysvětluje projektový koordinátor.
Zajímavou oblastí pro sběr dat z výroby jsou aplikace systémů optické kontroly a strojového vidění, tedy systémů, které zpracovávají obraz z kamer. „Pomocí nasbíraných obrázků jste schopni systém trénovat a zvyšovat spolehlivost rozpoznávání objektů. Z dlouhodobého hlediska můžete nalézt anomálie oproti původní trénovací sadě. Systém může pracovat spolehlivě, než se změní úhel dopadajícího slunce do haly nebo se v zorném poli kamery objeví cizí objekt. Sběr dat pomůže s případnou nápravou. Lze přidat zakrytování robotické buňky nebo mít dvě sady parametrů kamery, pro zimní a letní provoz. Vymyslet lze cokoliv,“ dodává.
Do budoucna bude pro výrobní podniky velkou výzvou umělá inteligence. „Naučit se, jak funguje, a pochopit, jak může pomáhat v procesech. K tomu ale potřebujete mít velké množství dat, bez nich nikdy fungovat nebude,“ říká Jan Václavovič z JHV Group.
„Více bude vstupovat do hry element umělé inteligence, ať už to bude strojové učení, diagnostika velkých dat, či prediktivní algoritmy. Bude jen na nás, zda data budeme chtít využívat, protože výrobní linky budou pracovat i bez nich. Jde ale o efektivitu a optimalizaci celého procesu,“ dodává.
Splynutí mobilních a IoT sítí
Zlepšit efektivitu a flexibilitu výroby mohou komunikační sítě 5G, zvláště tam, kde není možné použít kabelové připojení – mobilní roboty, automatizované dopravní systémy AGV. Současná průmyslová wi‑fi řešení již nejsou pro některé technologie dostačující, zvláště kvůli problémům se stabilitou připojení k síti.
„Zásadním momentem v rozvoji sítí 5G je jejich uzpůsobení pro aplikace v průmyslu, zvláště tam, kde je potřeba velice nízké zpoždění při přenosu,“ říká Jiří Vodrážka, vedoucí katedry telekomunikační techniky Fakulty elektrotechnické ČVUT v Praze.
Nejrůznější manipulátory a roboty je nutné centrálně řídit a mobilní síť je vhodným prostředkem pro komunikaci s nimi. „Je to z toho důvodu, že mobilní síť používá vyhrazené frekvence a je u ní daleko menší úroveň interferencí v porovnání s dnes běžně využívanými sítěmi wi‑fi,“ vysvětluje vedoucí katedry.
Jejich výhodou je také vysoká přenosová rychlost, která je důležitá například u pojízdných manipulátorů, které snímají veličiny s velkou rychlostí, případně při snímání obrazu. „Hlavním parametrem je nicméně rychlost odezvy. Zpoždění při přenosu je dnes v běžných sítích řádově ve stovkách milisekund, ale průmysl požaduje několik málo desítek milisekund. Druhým parametrem je spolehlivost sítě, aby nedocházelo k výpadkům,“ vysvětluje Jiří Vodrážka. Jakýkoliv výpadek komunikace může vést například k zastavení výkonu manipulátoru, pozastavení navazujícího procesu a zpoždění výroby.
Kromě mobilních sítí se rozvíjí komunikace mezi zařízeními v rámci internetu věcí (IoT). I pro něj je možné využít mobilní síť. „Pro internet věcí se budují specializované sítě s možností komunikovat s velkým množstvím zařízení,“ potvrzuje Jiří Vodrážka. „Do budoucna se předpokládá, že sítě internetu věcí budou s mobilními sítěmi nějakou dobu koexistovat a postupně splynou. Hlavní tíhu komunikace by měly v budoucnu převzít univerzální mobilní sítě,“ dodává vedoucí katedry telekomunikačních technologií.
Ten spolu se svými kolegy vyvinul sondu pro bezkontaktní sledování aktivity elektrických spotřebičů, která dokáže monitorovat odběr zařízení a data odesílat prostřednictvím sítě internetu věcí. „Testujeme ji pro lampy veřejného osvětlení v rámci chytrých měst, ale dá se použít i pro prediktivní údržbu. Pro sledování provozu stroje a předvídání míry opotřebení. Také se z ní dají získat data o spotřebě a tu pak optimalizovat,“ říká Jiří Vodrážka.
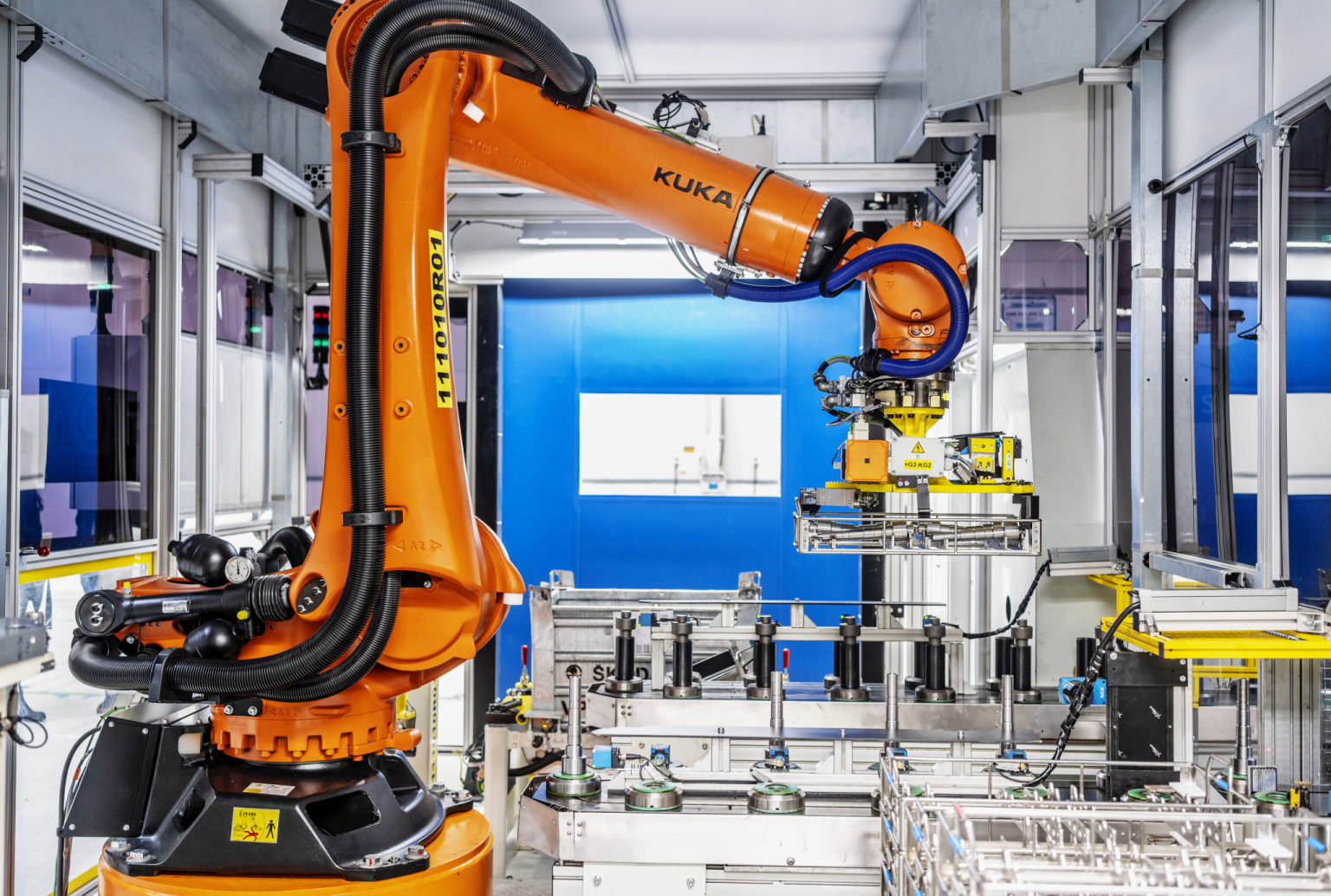
Projekt pozastaven
Současná ekonomická situace spojená s válkou na Ukrajině a vysokými cenami elektřiny vede k tomu, že firmy odsouvají projekty na využívání dat. „Není to tak patrné u velkých firem typu nadnárodních společností. U středních a ryze českých je to ale teď hodně znát. Některé projekty jsou pozastavené, vše se schvaluje několikrát, než se investice do technologie obnoví, a firmy zvažují, zda raději neinvestovat do jiné oblasti,“ říká Jan Václavovič.
Projekt na využívání dat zbrzdila pandemie a současná ekonomická situace například ve firmě IMS – Drašnar. Jde o rodinnou firmu, která vyvíjí a vyrábí produkty z plastu určené zejména pro autoprůmysl.
„Máme rozpracovaný software, který sbírá data ze vstřikolisů v reálném čase a umožňuje vyhodnocovat prostoje, zmetky, cykly a jednotlivé procesy výroby,“ říká Oto Vejda, výrobní ředitel IMS – Drašnar. „Projekt je pozastavený a vyčkáváme, jaká bude situace, protože jsme velmi závislí na automotive, kterému se v tuto chvíli nedaří tak, jak bychom si představovali,“ vysvětluje Oto Vejda.
Stáhněte si přílohu v PDF
Tato rodinná firma již nyní data z výroby využívá, ale v menší míře. Co se nyní musí zadávat ručně, půjde po spuštění projektu automaticky. „Očekáváme, že dojde k vyladění cyklu. Najdete slabá místa. Třeba když lis zastavuje u konkrétní výroby z nějakého důvodu. Pak budete statisticky schopni říct, že když odstraníte tento jeden prostoj, odstraníte 80 procent prostojů,“ říká výrobní ředitel.
Zesilujícím trendem je napojování jednotlivých strojů, informací o zaměstnancích, dodavatelských řetězcích a logistických procesech do jednoho systému, který dokáže jednotlivé datové sady analyzovat ve vzájemných souvislostech. V důsledku toho vznikají nová pracovní místa v různých oblastech firmy. „Jde hlavně o IT a robotizaci výroby. Nejvíce u nás v této oblasti firmy objednávají implementátory těchto řešení, specialisty na datové sklady a business intelligence platformy,“ potvrzuje Jiří Halbrštát, manažer náboru a marketingu ManpowerGroup.
Článek byl publikován ve speciální příloze HN Strojírenství.
Přidejte si Hospodářské noviny
mezi své oblíbené tituly
na Google zprávách.
Tento článek máteje zdarma. Když si předplatíte HN, budete moci číst všechny naše články nejen na vašem aktuálním připojení. Vaše předplatné brzy skončí. Předplaťte si HN a můžete i nadále číst všechny naše články. Nyní první 2 měsíce jen za 40 Kč.
- Veškerý obsah HN.cz
- Možnost kdykoliv zrušit
- Odemykejte obsah pro přátele
- Ukládejte si články na později
- Všechny články v audioverzi + playlist