Lisovna v automobilce Škoda Auto je srdcem výroby karoserie. Zde se z ocelových plechů lisují jednotlivé díly, které tvoří základ budoucího auta. Ve třech budovách lisovny se ročně spotřebuje přes 200 tisíc tun materiálu a z něj vyrobí téměř třicet milionů výlisků. Je tu devět lisovacích linek, tři nástřihové linky a přes 270 lisovacích nástrojů o hmotnosti až 50 tun.
Pro jednu z těchto hal aktuálně vyvíjí digitální dvojče. Systém, který bude přesně lokalizovat jakékoli problémy s energiemi a má za cíl ušetřit automobilce náklady, aktuálně skončil fázi testování a přechází do fáze produkčního projektu. „Měli bychom ho zavádět na konci příštího roku. Díky digitálnímu dvojčeti bude možné odhalit i úniky energií, na které bychom bez komplexního modelu budovy jen stěží přišli,“ říká Lukáš Altman Kousal, odborný koordinátor procesu lisování a automatizace ve Škodě Auto, který má v lisovně na starosti zejména digitalizaci. Jeho úkolem je převést zajímavé projekty do výrobního procesu.
„Technologie už jsou tak daleko, že dokážeme vytvořit digitální dvojče, dát ho do mobilního telefonu a propojit s daty v reálném čase. Budeme mít 3D model celého provozu, ‚helicopter view‘ nad celou budovou, doslova v kapse,“ dodává Altman Kousal.
Jak vypadá digitální dvojče v energetickém managementu a co všechno umí?
Projekt ŠKOTWIN (Škoda Auto Digital Twin) představuje průmyslové digitální dvojče pro průmyslové budovy. Toto digitální dvojče umožňuje nejen sledování, ale i zasílání lokalizovaných notifikací. Místo obecné zprávy „uniká voda“, dostanete detailní informaci „uniká voda v této části potrubí a přesně v této části haly“.
Odkdy bude systém v provozu?
Pokud půjde vše podle plánu, do konce příštího roku. Aktuálně máme k dispozici koncept tohoto systému, který bude následně implementován do našeho online prostředí. Nebude to nic jednoduchého, protože musíme řešit bezpečnostní prvky, aby byla aplikace bezpečná a dostupná pro všechny zaměstnance v různých úrovních přístupu. Aplikace je multiplatformní, což znamená, že ji lze spustit na jakémkoli operačním systému, ať už se jedná o počítače nebo mobilní zařízení. Graficky ji skvěle zobrazíte i na těch nejlevnějších telefonech.
Jaký je současný stav před nasazením digitálního dvojčete?
Používáme aplikaci zvanou Energis, která sdílí údaje z různých senzorů. Každá hala má hlavní senzor spotřeby budovy a několik dílčích senzorů. Aktuálně zpracováváme data v podobě číselných údajů, které uvádějí spotřebu energie, a vytváříme z těchto dat grafy a reporty. Tato data nejsou lokalizována na konkrétní místa v budově.
Takže když vám v tom grafu spotřeba vzroste proti normálu, nevíte přesně, v kterém místě je problém?
Víme číslo uzlu nebo měřiče, takže teoreticky víme, kde je problém. Například u měřiče 92031. Ale kde to přesně je? Samozřejmě máme energetické plány, 2D výkresy potrubí, ale upřímně řečeno, nejsou dostačující. Od digitálního dvojčete očekáváme, že celý systém bude plně zmapován a lokalizován na konkrétní místa. V současném energetickém plánu nemáme aktuální hodnoty spotřeby, pouze identifikátory měřičů. Pokud chceme zjistit, zda došlo ke zvýšení nebo snížení spotřeby, musíme přejít do jiného systému a hledat data tam.
Jak dlouho v současnosti trvá vyřešení problému od chvíle, kdy ho zjistíte?
První krok byl, že jsme měli pouze surová data v grafech, manuálně jsme kontrolovali problémy a v případě potřeby jsme si nastavili jednoduchou notifikaci. Druhým krokem bylo zapojení systému, který sleduje výkyvy energie. Jedná se o silný nástroj pro reporting. Když si kliknu na konkrétní den, vidím aktuální spotřebu energií. Například fialová křivka představuje reálnou spotřebu, která je přepočítána na jednotlivé zdvihy lisovacích linek, takže když nevyrábíme, tak se i očekává nižší spotřeba. Zelená křivka představuje modelovanou, predikovanou spotřebu na základě předchozího období.
Tento systém nám umožňuje porovnávat dvě stejná období, například celozávodní dovolené nebo sezony jako podzim či Vánoce, a generovat reporty.
Aktuálně když zjistíme nějakou anomálii, například zvýšenou spotřebu vzduchu po celozávodní dovolené, musíme přejít do jiného systému, zjistit konkrétní měřič a číslo a poté se podívat do layoutu, abychom zjistili, kde přesně se problém nachází. S digitálním dvojčetem budeme schopni propojit všechny tyto informace, aby systém okamžitě identifikoval anomálii na konkrétním místě a ukázal, o jak velký problém se jedná. Jinými slovy, digitální dvojče by mělo přinést okamžitou informaci o anomáliích přímo z grafů a přesně je lokalizovat.
Předpokládám, že když nakupujete svítidla a podobně, máte už od výrobce chytré systémy, které vám spotřebu hlídají a hlásí, kde přesně je problém.
Ano, například při instalaci nového LED osvětlení jsme od výrobce dostali aplikaci, která nám umožňuje sledovat, kde jaké světlo svítí, jestli svítí, kolik má energie a podobně. Nicméně jde o další samostatný systém. Cílem digitálního dvojčete je integrovat všechny tyto různé systémy do jednoho.
Kde nejčastěji bývají v lisovně úniky energií?
Nejčastější úniky energií se objevují v oblasti stlačeného vzduchu. Lisovací linky využívají stlačený vzduch k přenosu výlisků pomocí systémů s přísavkami. Tento proces nese vysoké riziko úniků stlačeného vzduchu, jenž je v podstatně nejdražším médiem, které spotřebováváme. Navíc se únik špatně detekuje. I když ho provází syčivý zvuk, v lisovně je relativně velký hluk, takže lidé v provozu si často ani nevšimnou, že k němu dochází. Ztráty jsou přitom citelné.
Jak se o únicích stlačeného vzduchu tedy dozvíte?
Máme v podstatě dvě hlavní metody pro zjišťování úniků. První z nich jsou měřiče, které nám ukazují spotřebu stlačeného vzduchu. Druhá metoda přijde s implementací digitálního dvojčete. Plánujeme instalovat měřiče na jednotlivé celky, například na všechny lisovací linky a na celou dílnu, ve které jsou všechny nástroje poháněné stlačeným vzduchem. To nám umožní lépe lokalizovat úniky. Například i světlíky na stropě jsou ovládány stlačeným vzduchem, a když tam uniká vzduch, málokdo si toho všimne. Díky měřičům a digitálnímu dvojčeti bychom mohli přesně určit, odkud únik pochází.
Další varianta zahrnuje použití akustické kamery, která pomocí zvukového přenosu zjistí úniky vzduchu a zobrazí je na snímku pomocí barevného znázornění na přehledném displeji. Tyto informace můžeme ručně zadat do digitálního dvojčete, včetně připojení obrázku, a tím přesně určit místo úniku. Systém by měl být schopen propojit tato data s dalšími systémy, které například řeknou, že už údržbář problém opravil.
Jak vypadá vývoj digitálního dvojčete? Co všechno je potřeba nahrát, nasnímat?
Abyste mohli vytvořit digitální dvojče, potřebujete platformu, do které se nahrávají jednotlivé 3D modely. Je to podobné, jako když vytváříte prezentaci v PowerPointu. V tomto případě ale potřebujete platformu pro digitální dvojče. Prvním krokem je vytvoření modelu budovy. Do haly se postaví lidarový skener, který se otáčí a vytváří přitom takzvané mračno bodů. Z něj pak vymodelujeme přesný vektorový model budovy. Jednotlivé části popíšeme a pojmenujeme – tohle jsou lisy, tohle lisovací nástroje, tohle palety. K popsanému modelu navážeme takzvané body zájmu, které označují konkrétní komponenty, a ty jsou propojeny se senzory. Když vyvíjíte digitální dvojče, potřebuje zdroj dat, takže ho musíte propojit se stávajícími systémy – se systémem, který dává informace o spotřebě energií, s výrobními daty, s logistickým systémem a podobně.
Takže dokážete sledovat každý stroj, kabel a každý detail lisovny?
V případě, že jsou na nich umístěné senzory nebo měřiče. Ty samozřejmě nemáme úplně všude, protože by to bylo nehospodárné. Jsou na místech, kde to dává smysl.
Kolik je v lisovně senzorů?
Několik stovek.
Narazili jste v rámci testování digitálního dvojčete na nějaké skryté úniky?
Ano, máme jeden hezký příklad. I když náš tým zná lisovnu velice dobře a staráme se o ni, objevili jsme něco, co nám uniklo. Při kreslení systému chlazení pro digitální dvojče jsme zjistili, že nám protéká chladicí voda volným okruhem. Zádrhel byl v tom, že nevytékala na zem, prostě vtekla do budovy a rozdělila se – část chladila lisovací linku a část proudila do volného okruhu. Protekla okruhem, aniž by byla nějak využita.
Takovýmto ztrátám by se nedalo jinak zabránit? Neměli byste šanci je zjistit?
Dalo by se to zjistit, ale museli bychom projít všechna data, jestli náhodou nemáme vyšší spotřebu. Ale když dlouhodobě byla spotřeba stále stejná, nikoho nenapadlo hledat problém. Až v momentě, kdy jsme začali kreslit digitální dvojče, zjistili jsme, že existuje nějaká otevřená větev v okruhu. Zavřeli jsme ji, snížil se průtok a voda už chladí jen stroje a neprotéká volnou větví.
Co se tedy stane, když někdo zapomene zavřít třeba logistická vrata? Jak na to bude reagovat nový systém?
V rámci digitálního dvojčete a nasazení do online prostředí chceme dát na logistická vrata senzory, které nám řeknou, zda jsou dveře otevřené, nebo zavřené. Systém bude počítat čas mezi otevřením a zavřením, který by měl být přibližně dvacet sekund. To je doba, která stačí na projetí vysokozdvižného vozíku.
Pokud dveře zůstávají otevřené déle, než je nastavený limit, například více než 150 procent normálního času, systém zašle notifikaci o tom, že dveře nebyly zavřeny. To je důležité zvláště v zimních měsících, aby studený vzduch proudící do haly nezvyšoval náklady na vytápění.
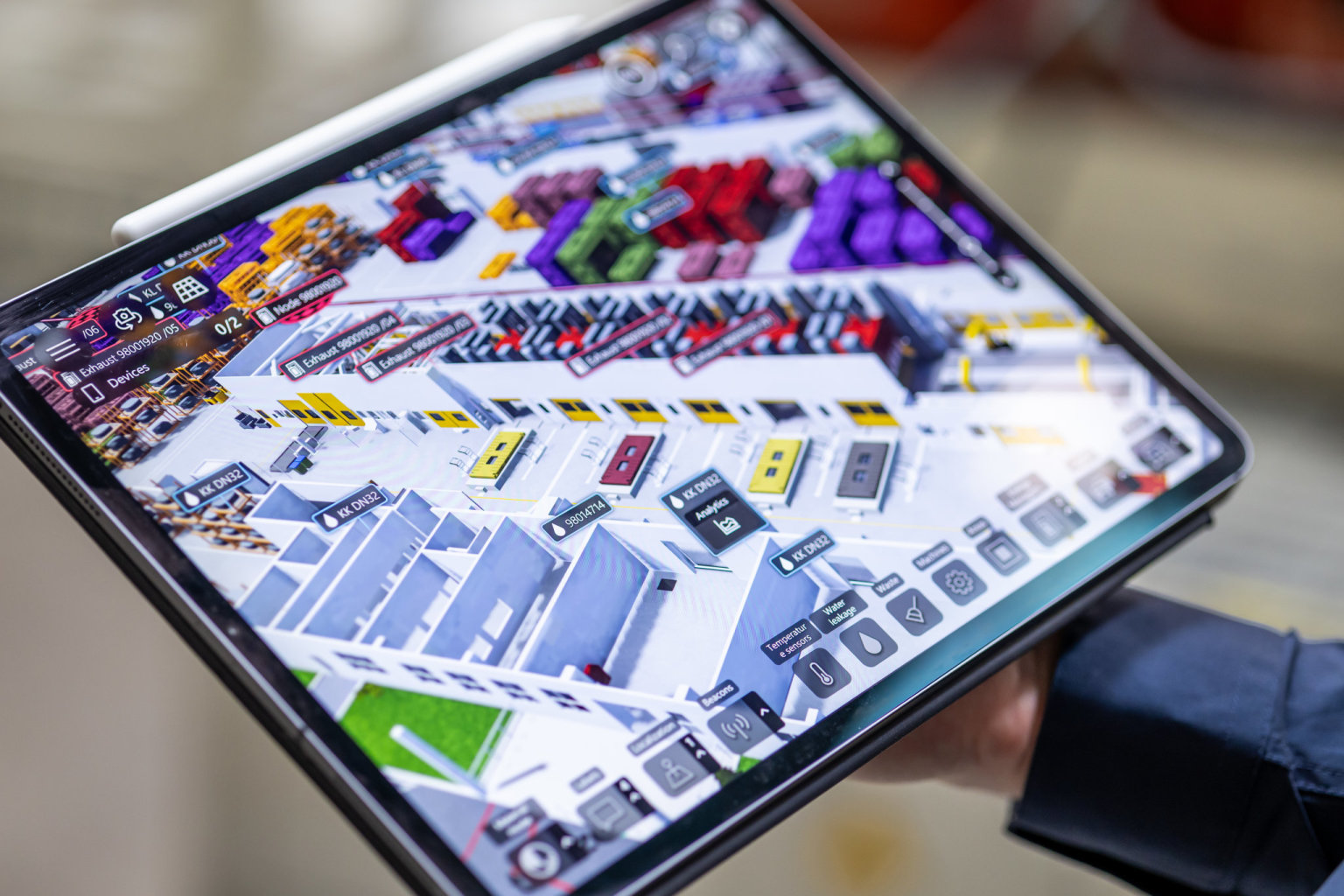
Kde vidíte největší přínos digitálních dvojčat v energetickém managementu?
Největší přínos je v rychlé lokalizaci úniku, na který můžete velmi rychle zareagovat. Když ještě nyní nemám digitální dvojče plně nasazené, musím úniky dohledávat. Každé pondělí se dívám na energie, porovnávám je a případné úniky dohledávám. Tím ale utíká čas, který při úniku vody nebo stlačeného vzduchu může být hodně drahý.
S plně nasazeným digitálním dvojčetem mohu rychle identifikovat neobvyklé zvýšení spotřeby, například pitné vody v kancelářích, nebo daleko rychleji lokalizovat, kde protéká záchod. To je mimochodem častý problém, ale málokdo ho nahlásí.
Digitální dvojče umožní detekovat problémy i během odstávek či celozávodních dovolených, kdy je budova prázdná, ale může docházet k únikům.
Vše navíc můžete kontrolovat klidně z Havaje.
Až budeme mít plně nasazené digitální dvojče, tak i z Havaje. Už nyní máme digitální dvojče lisovací linky, a když jsem byl na služební cestě v Izraeli, sledoval jsem, jak linka lisuje a jaké má závady. Pro zodpovědnou osobu je vzdálený přístup super.
V halách máte i stroje, které jsou několik desítek let staré. U nich předpokládám, že budou notifikace vyskakovat často. Jak s tímto problémem budete pracovat?
To bude platit pro staré linky, na kterých jsou senzory. Většinou na těch nejstarších žádné nemáme a jsou jen na kritických místech, která mohou ohrozit výrobu. Například kontrolu stlačeného vzduchu u staré linky děláme pomocí sonické kamery, a ne pomocí senzorů, protože počítáme s tím, že ji brzo budeme modernizovat. Ale samozřejmě že alarmů u jiných starších zařízení může být spousta a budeme to muset vyřešit sdruženými notifikacemi. Jednoduše přijde jedna notifikace, ve které bude informace například o pěti místech, na kterých se něco děje.
Jakou roli v novém systému bude hrát umělá inteligence?
Bude porovnávat aktuální spotřebu s modelovou, a jakmile se od sebe odliší, ihned nahlásí „pozor, něco se tady děje“.
Jaké jsou nevýhody digitálních dvojčat?
Nevýhodou je, že vždy když digitální dvojče modelujete, vytváříte 3D model k určitému časovému okamžiku. Ve chvíli, kdy halu přestavíte, digitální dvojče se samo nepřestaví a celé kolečko musíte udělat znovu. Takže už nyní řešíme, jak budeme dělat update. Můžeme to dělat manuálně, například pomocí lidarového skeneru, kdy technik oskenuje prostor a nahraje nové údaje do systému. Uvažujeme i nad využíváním autonomních robotů, jako je známý žlutý robotický pes od Boston Dynamics, který je vybavený lidarovým skenerem. Tento robot by mohl prostor oskenovat a aktualizovat 3D model. V dalších fázích projektu bychom chtěli nasadit drony, které by dělaly inspekci střech a hlásily by případné díry nebo nedovřené světlíky, které představují energetické ztráty.
Pro naši lisovnu je aktualizace relativně jednoduchá, protože máme jeden velký lisovací stroj a jednoduchou strukturu haly. Když se změní stroj, tak se v rámci digitálního dvojčete jen změní obálka toho stroje, což je relativně snadný update. Ovšem v halách, jako je montáž nebo svařovna, kde se mohou změnit celé výrobní linky, je aktualizace digitálního dvojčete mnohem náročnější.
Budete systém zavádět i v jiných halách?
Mojí vizí je systém napřed zavést v lisovnách, potom v lakovnách a následně ve všech provozech. Naším cílem je mít digitální dvojče celého areálu a mít energie pod kontrolou nad celým závodem.
Lukáš Altman Kousal (38)
Je absolventem Fakulty strojní Vysoké školy báňské – Technické univerzity Ostrava. Do Škody Auto nastoupil v roce 2011 jako specialista na NC programování. V lisovně je od roku 2017, aktuálně na pozici odborný koordinátor procesu lisování a automatizace.
Pro lisovnu Škody Auto hledá technologické novinky, které mají zefektivnit výrobu a usnadnit zaměstnancům práci. Aktuálně pracuje hlavně na implementaci digitálního dvojčete v energetickém managementu.
S nadšením testuje nové technologie od AI až po virtuální realitu. Staví si chytrou domácnost. Spoluzaložil a moderuje podcast Biomorfní průmysl.
Jakou vidíte budoucnost digitálních dvojčat ve vašem oboru?
Budoucnost vidím v nasazení umělé inteligence, která by dokázala řídit celý výrobní proces. Díky strojovému vidění by mělo digitální dvojče informace i o logistice. Při výskytu problému, například když se zaseknou logistická vrata, by algoritmy dokázaly okamžitě předpovědět, jak bude tento problém ovlivňovat výrobu. Digitální dvojče by mohlo okamžitě identifikovat, že kvůli zaseknutým vratům nebude možné dodat výlisky do svařovny, tím pádem svařovna nedodá montáži a auto se reálně nevyrobí. Digitální dvojče bude moci dopředu predikovat, jak dlouho si můžeme dovolit nechat vrata zavřená, než zastavíme výrobu.
Dnes se podobné problémy řeší tak, že plánovači rychle zkontrolují stav zásob a podají informaci, jak dlouho mohou vrata zůstat zavřená, než se zastaví výroba. S pomocí umělé inteligence bychom mohli získávat tato data automaticky a okamžitě. Systém by mohl třeba vědět, jak to ovlivní celý výrobní tok, když firma opraví vrata například za 35 minut.
Stáhněte si přílohu v PDF
Můžete uvést ještě jiný příklad využití digitálního dvojčete?
Digitální dvojče nemusí sloužit jen pro účely energetického managementu, ale například i na sledování lisovacích nástrojů. Reálně se můžeme jít do haly podívat a zjistit, kde se který nástroj nachází, ale lepší je to vidět digitálně a sledovat jejich pohyb v reálném čase. Chceme například vědět, kolik času strávily na údržbě a zda byla oprava skutečně provedena. V rámci kritického plánování nám algoritmy mohou pomoci v případě, že se porouchá linka a nástroje bude potřeba převézt do jiné haly. V závislosti na tom, kde leží, to může trvat i tři hodiny, protože každý má kolem padesáti tun. A s každým prodlením zbytečně naskakuje čas.
V případě, že lisovací linka zůstane nefunkční na několik dní a my nemáme dostatek zásob, je klíčové vědět, jak rychle můžeme nejkritičtější nástroj dostat do provozu jinde. Místo obvolávání a zjišťování chceme tyto informace mít okamžitě dostupné pomocí algoritmů. Právě monitoring lisovacích nástrojů je jeden z dalších projektů, který plánujeme u digitálních dvojčat.
Jaké jsou další vaše vize a plány?
Jednou z našich vizí je udělat v budoucnu z jedné naší haly lisovny takovou testovací laboratoř. Osadit ji co nejvíce senzory, testovat různé způsoby jejich využití a výsledky nabízet do dalších provozů. Chtěl bych i více experimentovat s teplotními senzory a prouděním vzduchu, abychom dosáhli rovnoměrného vytápění celé haly. Znamenalo by to zjistit, v jakých částech haly teplotu snížit a kterou naopak vytápět více. Přemýšlíme nad spoustou projektů, které bychom rádi realizovali ideálně ve spolupráci s nějakou univerzitou.
Článek byl publikován ve speciální příloze HN Automatizace a robotizace.
Přidejte si Hospodářské noviny
mezi své oblíbené tituly
na Google zprávách.
Tento článek máteje zdarma. Když si předplatíte HN, budete moci číst všechny naše články nejen na vašem aktuálním připojení. Vaše předplatné brzy skončí. Předplaťte si HN a můžete i nadále číst všechny naše články. Nyní první 2 měsíce jen za 40 Kč.
- Veškerý obsah HN.cz
- Možnost kdykoliv zrušit
- Odemykejte obsah pro přátele
- Ukládejte si články na později
- Všechny články v audioverzi + playlist