Největší výzvou digitalizace není vytváření dat, ale schopnost porozumět jim a dokázat je co nejlépe využít, říká Cedrik Neike, člen představenstva Siemens AG a CEO divize Digital Industries. Jednou z cest je digitální dvojče – přesná datová kopie produktu, továrny nebo celého dodavatelského řetězce. Díky digitálnímu dvojčeti je možné výrobu přizpůsobit například pandemii v řádu několika hodin. Nebo dokonce zmírnit ekologickou stopu výrobku. Česko je pro Siemens jednou z klíčových zemí, a to nejen ve výrobě, ale také ve výzkumu a vývoji, říká Neike.
Společnost Fast Company, která se zaměřuje na globální inovace, vyhlásila letos Siemens firmou, jež hýbe světem (World Changing Company). Siemens ocenění získal především díky svému pokroku v digitalizaci. Co vy osobně na digitalizaci vidíte jako nejvíc obtížné?
S digitalizací je problém ten, že jsme velmi, velmi dobří ve vytváření dat, ale už je neumíme moc dobře používat. Dám konkrétní příklad: továrna, taková, jako máme v Česku, vytvoří měsíčně zhruba 2200 terabajtů dat. Aby si to čtenáři dokázali představit, je to zhruba jako půl milionu filmů na Netflixu v čistě datové podobě. Je to tedy obrovské množství dat, které se denně vytvoří, ovšem většina z nich se nikdy k ničemu nevyužije. Kouzlo digitalizace spočívá v tom, najít způsob, jak z těch dat získat něco smysluplného. Největší výzvou digitalizace tedy není vytváření dat, ale porozumět jim a přetvořit je ve smysluplný a využitelný nástroj. Jako příklad můžu uvést start‑up GreenTech, který ve vertikálních farmách hydroponicky pěstuje salát a používá naše IoT technologie. Samozřejmě snahou je ušetřit co nejvíce vody, emisí CO2 i pesticidů, takže pěstování například salátů se musí konstantně monitorovat. Je to krásný příklad toho, jak správné využití dat pomáhá vytvořit něco hyperefektivního.
Rostoucí cena energií digitalizaci nezastavila
Vaše továrna v Ambergu v Bavorsku, která pochází z 80. let, byla nedávno vyhlášena za nejmodernější a nejvíce digitalizovanou továrnu na světě. Díky čemu?
Hlavním důvodem je, že se stejným počtem lidí a stejnou výrobní plochou dosáhl závod čtrnáctinásobného zvýšení objemu výroby a zlepšil kvalitu výroby. Jednoduše díky tomu, že dokáže reagovat extrémně rychle. Produkty vyráběné v téhle továrně jsou kompletně digitální, mají takzvané digitální dvojče. Když jsme například měli problémy s dodávkami mikročipů, díky digitálnímu dvojčeti jsme dokázali během dvou dnů změnit konstrukční návrh našeho produktu a poté naprogramovat továrnu tak, abychom získali požadovaný výstup. Digitální dvojče nám umožnilo reagovat mnohem rychleji než kdokoli v našem oboru.
V jedné z našich největších továren v Mohelnici používáme data k predikci údržby strojů. Díky datům předem víme, že stroj může mít technický problém, a proto můžeme naplánovat odstávku dříve, než se stroj rozbije nebo vážně poškodí. Obecně lze říct, že takto je možné zredukovat náklady na opravy strojů až o 20 procent.
Pořád se tak vracíme k hlavní myšlence: vtip není v tom, produkovat data, ale sbírat je a dokázat je smysluplně využít, ať už k efektivnějšímu pěstování salátů, k výrobě chybějících součástek díky digitálnímu dvojčeti nebo k lepší údržbě strojů.
A zavádíte tyto digitální inovace také v Česku?
Ano. V Česku máme několik klíčových továren, například v Trutnově, kde používáme takzvaný condition monitoring (jde o sběr a inteligentní analýzu dat z výrobních strojů, systém pomáhá odstranit zbytečné prostoje ve výrobě, optimalizuje výrobní procesy, odhaluje problémy a pomáhá pochopit jejich příčiny, pozn. red.). V závodě v Letohradě zase používáme interní výrobní informační systém s prvky umělé inteligence, který pomáhá zvyšovat kvalitu a produktivitu výroby. Ve Frenštátu zase sdružujeme data do cloudu a díky tomu je optimalizujeme. Většina lidí neví, že každý třetí výrobní stroj na světě má řídicí systém ze Siemensu. Máme největší továrnu na výrobu řídicích systémů na světě. V českých továrnách využíváme naše nejmodernější technologie a jsou v digitalizaci velmi pokročilé.
Český trh se stejně jako většina evropských trhů potýká s nedostatkem techniků a IT specialistů. Plánujete v Česku otevřít nová vzdělávací střediska pro tyto obory?
Absolutní nedostatek IT specialistů panuje všude na světě. Školy jich jednoduše nedokážou produkovat dostatek. Poradit si s tím lze dvěma způsoby: můžete vycvičit vlastní lidi v rámci vaší společnosti, otevřít vlastní tréninková střediska. Já sám jsem například začínal jako praktikant ještě předtím, než jsem nastoupil na vysokou školu. Ale zároveň musíme technologie zjednodušit. Nyní například pracujeme na platformě Mendix, která funguje na low‑code nebo no‑code principu. Jeho myšlenka spočívá v tom, že já, vy, kdokoliv může vytvořit program, protože používat IT nástroje je zde velmi jednoduché. Tedy snažíme se trénovat nové lidi a zjednodušovat technologie. Dám příklad: uzavřeli jsme strategické partnerství se společností Mercedes‑Benz. Vzali jsme si na paškál jednu z jejich nejstarších továren v Berlíně, kompletně jsme ji zdigitalizovali, posunuli jsme ji směrem k zeleným technologiím a pomohli přeškolit jejich zaměstnance tím, že jsme je vybavili low‑code/no‑code dovednostmi.
Jak významné je vlastně pro Siemens Česko?
Velmi. A nejen z toho pohledu, že v Česku máme velmi pokrokové a velmi efektivní továrny, které se mohou klidně srovnávat s ostatními světovými továrnami, ale také proto, že více než tisíc zaměstnanců, což je deset procent našich zaměstnanců v Česku, pracuje ve výzkumu a vývoji. Siemens je jedním ze tří hlavních přihlašovatelů patentů v Evropě a velká část našeho vývoje elektromotorů spadá právě do Česka. Takže je pro nás důležité nejen jako výrobna, ale také jako centrum výzkumu.
A plánujete v Česku otevřít ještě další vývojová střediska?
Již nyní máme v Česku několik vývojových středisek, dvě v Praze, jedno v Brně, dvě v Ostravě a dvě v Plzni. Když porovnám populaci s investicemi do výzkumu a vývoje, je Česko jednou z předních zemí Siemensu. Vlastní vývojová centra mají i výrobní závody Siemens v Česku.
Cedrik Neike (49)
člen představenstva a CEO divize Digital Industries, Siemens AG
Narodil se v Berlíně, ve Francii vystudoval evropskou obchodní školu INSEAD.
V Siemensu začal pracovat v roce 1997 jako produktový manažer se zaměřením na bezdrátový internet. Šestnáct let působil také v Cisco Systems.
V roce 2017 se do Siemensu vrátil a nyní je členem jeho představenstva.
Působí jako CEO divize Digital Industries. Odpovídá za Siemens Advanta (výzkum, vývoj a poradenství v oblasti digitalizace), IT a Cybersecurity.
Žije v Berlíně, je ženatý, má čtyři děti.
Jeho koníčkem je turistika, do práce jezdí na kole za každého počasí.
Zmínil jste pojem digitálního dvojčete, které je pro digitalizaci stále důležitějším nástrojem. Jak přesně s ním pracujete a jak vám pomohlo například v pandemii?
V zásadě existují tři typy digitálních dvojčat. Jedno vzniká, když vyrobíte nový produkt, obsahuje informace o jeho výrobních vlastnostech. Dále se dělá digitální dvojče továrny, které obsahuje hlavně informace o jejích provozních vlastnostech. A také existuje digitální dvojče používání produktu. Dám k tomu příklad z naší továrny v Ambergu: když se stane, že některý z mikročipů není k dispozici, vezmeme jiný mikročip a pomocí digitálního dvojčete výrobku můžeme zjistit, zda nový mikročip vyhovuje, nebo zda jej musíme upravit. Tedy pokrytí výpadku mikročipů je mnohem rychlejší. Díky tomu, že máme digitální dvojče továrny, můžeme potom změnit nastavení provozu továrny během pár hodin. Můžeme se rozhodnout, že budeme používat jeden komponent raději místo jiného. A to je velmi důležité – továrny, které mají digitální dvojče, jsou mnohem lepší v reakci na aktuální situace, například právě během pandemie. V továrně jednoho vietnamského konglomerátu, který vyráběl smartphony, jsme díky digitálnímu dvojčeti pomohli přenastavit výrobu během tří týdnů tak, aby mohli vyrábět respirátory. Dokázali pak vyrábět padesát tisíc respirátorů měsíčně. Tedy digitální dvojče umožňuje reagovat extrémně rychle a také mnohem rychleji uvádět produkty do výroby.
Jak chcete technologii digitálního dvojčete dále rozvíjet?
V současnosti máme tisíce malých digitálních dvojčat: například jak produkt pracuje mechanicky, jaké má fyzikální vlastnosti a tak dále. Chceme to ale zjednodušit a místo tisíců dílčích digitálních dvojčat chceme vytvořit jedno holistické, ucelené. Výhodou bude mimo jiné mnohem menší náročnost na data. Nyní to funguje tak, že vytvoříte digitální dvojče a odešlete data o něm. Vytvoříte další a odešlete další data. Chceme ale, aby se data integrovala, sbírala na jedno místo. Digitální dvojče byste tak mohli spustit během výroby – ale rychleji než výrobu. Takže již během výroby budete moci simulovat změny ve výrobku, zvolit tu nejlepší verzi změny a zavést ji do produkce. V budoucnu to tedy bude holistický typ dvojčete v real‑time podobě.
Může digitální dvojče nějak napomoci udržitelnosti ve výrobě?
Ano, rádi bychom zabudovali digitální dvojče do dodavatelského řetězce, aby integrovalo všechny dodavatele dané firmy. Proč? Je to velmi důležité právě pro udržitelnost. Můžete si totiž vytvořit zelené digitální dvojče. Můžete například říct: náš motor, který se vyrábí v Mohelnici, se bude vyrábět jen pomocí zelené energie, bude pro něj zapotřebí jen velmi málo emisí CO2. Takže když někdo například v Německu bude motor integrovat do svého zařízení, tak bude vědět, jak se ten motor vyráběl, a bude moci potvrdit, že tenhle motor z Česka byl opravdu vyroben udržitelným způsobem. A bude to moci vzkázat i svým zákazníkům. Jednoduše údaje rozšíříte do svého dodavatelského řetězce, to je velká výhoda takzvaného zeleného digitálního dvojčete.
A jak daleko jste se zaváděním holistického dvojčete?
Už jsme jej otestovali na pár místech, například v naší továrně v Ambergu. V současnosti používá běžná digitální dvojčata zhruba 11 procent společností na světě a pouze malá část z nich využívá tuto holistickou podobu. Ale jeho využívání se nyní velmi rychle rozšiřuje, a to i díky pandemii koronaviru. V podstatě nám firmy řekly: Prosím pomozte nám s vývojem digitálního dvojčete co nejrychleji. Celkově bych digitalizaci přirovnal k lahvi s kečupem. Dlouho s ní třesete a třesete, ale nic nejde ven, žádný výsledek. A nyní, zhruba deset let po zavedení pojmu průmysl 4.0, se všichni vrhají na digitalizaci jako diví. Během uplynulých tří krizí, tedy pandemie koronaviru, války na Ukrajině a nyní krize se zdražováním plynu a pohonných hmot, a samozřejmě také v nutnosti přejít na udržitelnou výrobu firmy zjišťují, že skutečně potřebují zavést do své výroby změny.
A vy tuto technologii prodáváte ostatním společnostem?
Ano, již nyní ji například prodáváme výrobcům baterií. V jedné z těchto továren na baterie například holistické digitální dvojče pomáhá navrhovat a vyrábět lepší baterie a stejně tak jim pomáhá v lepším plánování recyklace baterií. Digitální dvojče jednoduše umožňuje uzavřít celý životní cyklus produktu. Víme, jak se baterie vyrobila, a víme, jak v autě pracuje. Takže když některá část baterie přestane fungovat, dá se ta jednotlivá část vyměnit a samozřejmě na konci se dá lépe recyklovat. Stejně tak se holistická digitální dvojčata uplatňují v potravinářském a nápojovém průmyslu a v dalších odvětvích. Česko, stejně jako další evropské státy, nemá rostoucí, nýbrž stárnoucí populaci. Jeho odpovědí na stárnutí pracovní síly by tedy měly být investice do technologií, aby se udrželo konkurenceschopné.
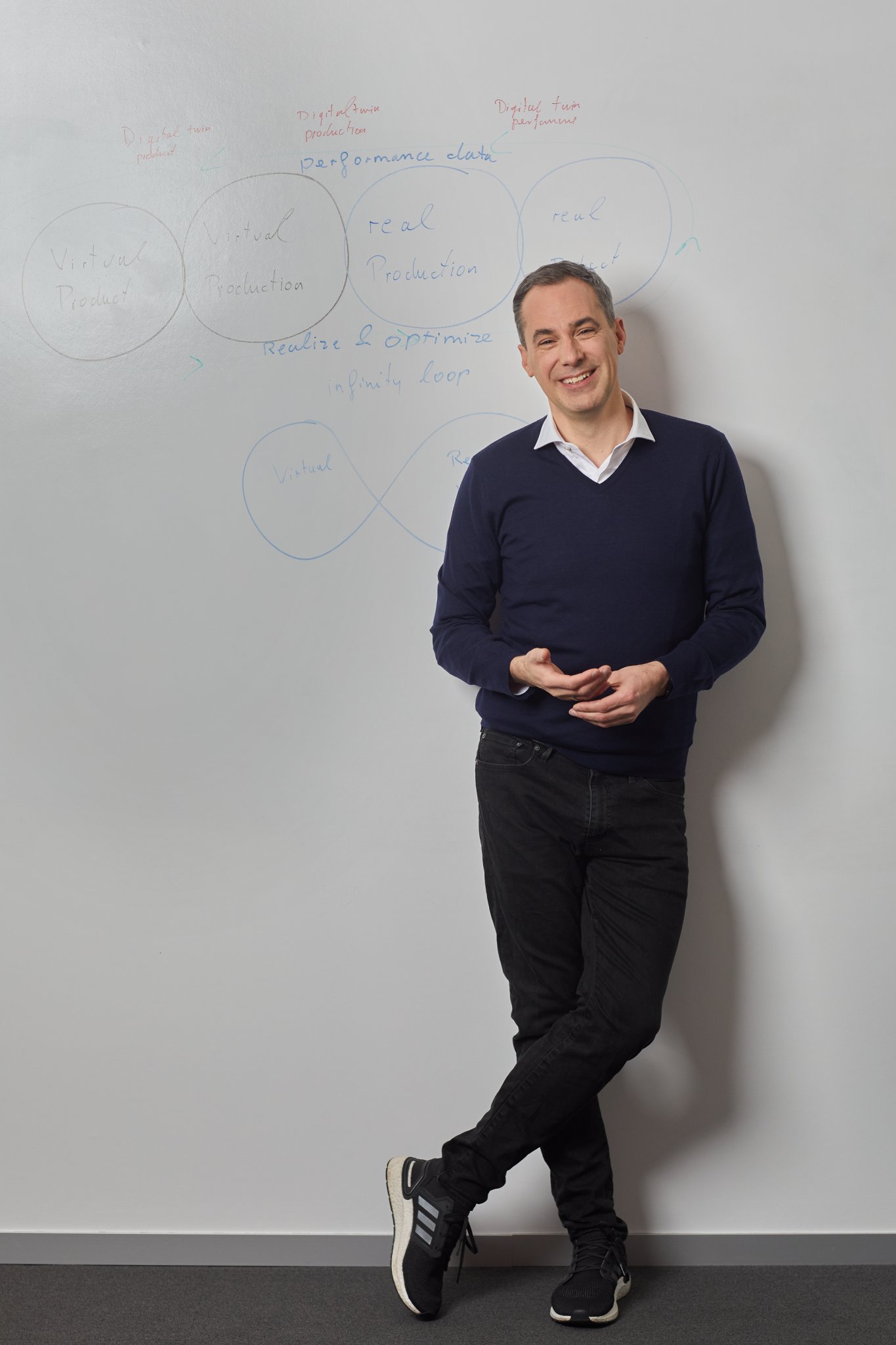
Na jakých dalších digitálních inovacích ještě v Siemensu pracujete?
První zásadní věcí je něco, čemu říkáme Cloud and Edge. Amazon, Microsoft a mnoho dalších velkých firem pracuje na cloudu. My nyní spolupracujeme se všemi velkými poskytovateli cloudů a vyvíjíme Xcelerator (otevřenou digitální obchodní platformu, která urychluje digitální transformaci – různě velké společnosti mají přístup k různým digitálním technologiím napříč doménami, pozn. red.). Dejme tomu, že máte na světě pětadvacet továren a z toho dvacet v Česku. Data z nich uložíte do cloudu a jednotlivé továrny můžete vylepšovat, protože je porovnáváte s těmi nejlepšími.
Druhá naše aktuální inovace se týká edge computingu. Jsme přesvědčeni, že spousta dat z továren zůstává ve skutečnosti v továrnách, kde vznikla, a nikdy se do cloudu nedostanou. Proč? Protože nechcete pravidelně každý měsíc nahrávat do cloudu pět set tisíc netflixových filmů. Takže musíte získat technologii, která vám pomůže využívat tato data na místě, kde vznikají. Budete se pak moci například na 90 procent dat podívat přímo v zařízení a jen deset procent pošlete do cloudu. No a další naše technologie bude pracovat s umělou inteligencí. Pokud tedy máte data jako z pěti set tisíc filmů měsíčně, tak to není práce pro člověka, nýbrž pro umělou inteligenci. Ta je projde a zjistí, jak by se dala lépe řadit a optimalizovat.
Stáhněte si přílohu v PDF
Společně s digitalizací a množstvím dat online přichází také velmi citlivá otázka ochrany firemních dat. Jak ji mají firmy řešit?
Musí být v kyberbezpečnosti extrémně silné a vždy tak trochu paranoidní, aby ochránily svůj vlastní majetek i majetek svých zákazníků. Pokud si některá firma myslí, že už je v kyberzabezpečení dobrá a že má vše v pořádku, je to moment, kdy přestává myslet na to, co by se mohlo stát, co jí hrozí. S tím, jak posíláme do online prostoru stále více dat, elementů, na které je možné útočit, stále přibývá. Firmy tedy musí klást na kyberbezpečnost stále větší důraz.
V Siemensu vedete také oddělení kyberbezpečnosti. Jak se Siemens vyrovnává s kyberhrozbami?
Děláme pro to hned několik věcí. Za prvé stále pokračujeme v rozšiřování kyberbezpečnostních prostředků a pozorně se zaměřujeme na přínosy každého z nich. A stejně tak zastáváme koncept Zero Trust, tedy nulové důvěry. Znamená to, že místo abychom měli za jedněmi zamčenými dveřmi zavřené všechno, vždy pracujeme pouze s jednotlivou částí informací. Takže nemůžete prostě vejít a získat přístup ke všemu, informace jsou oddělené. Za druhé, kyberbezpečnost nebudujeme sami, ale s partnery. Vytvořili jsme něco, čemu říkáme Charter of Trust (Charta důvěry je nezisková aliance, kterou inicioval Siemens. Vyžaduje závazná pravidla a standardy v kybernetické bezpečnosti, pozn. red.). Je to společenství sedmnácti největších firem, s nimiž jsme ustavili společné kyberbezpečnostní principy. Tedy co funguje u nás, to bude fungovat i u vás a budeme na zabezpečení našich dat pracovat společně. Abych to shrnul – kybernetická bezpečnost je a bude stále důležitějším tématem a je třeba v tomto ohledu být paranoidní. Za druhé musíte vybudovat architekturu zabezpečení informací, kde jednotlivé části budou na sobě nezávislé. A musíte pracovat v ekosystému.
Článek byl publikován ve speciální příloze HN Automatizace a robotizace.
Přidejte si Hospodářské noviny
mezi své oblíbené tituly
na Google zprávách.
Tento článek máteje zdarma. Když si předplatíte HN, budete moci číst všechny naše články nejen na vašem aktuálním připojení. Vaše předplatné brzy skončí. Předplaťte si HN a můžete i nadále číst všechny naše články. Nyní první 2 měsíce jen za 40 Kč.
- Veškerý obsah HN.cz
- Možnost kdykoliv zrušit
- Odemykejte obsah pro přátele
- Ukládejte si články na později
- Všechny články v audioverzi + playlist