Nahrát do obráběcího stroje konstrukční model obrobku a stroj si již sám navrhne způsob, jakým bude dílec obrábět. Tímto směrem se nyní ubírá vývoj digitálních dvojčat v obrábění. Tedy jakýchsi virtuálních dvojníků výrobků, strojů i celých výrobních procesů. Již v současnosti nacházejí stále větší uplatnění v průmyslových aplikacích. Pandemie jejich význam posílila a umocnil ho trend digitalizace, který je patrný s příchodem Průmyslu 4.0.
Doba, kdy každé výrobní zařízení bude mít své virtuální dvojče, již není příliš vzdálená. Navíc se aplikace stále zjednodušují. Zatímco v současnosti jsou vzhledem k vysokým požadavkům na odborné znalosti pracovníků a nákladnému zavádění dosažitelné především pro velké firmy, postupně se stanou dostupnějšími i pro malé a střední podniky a budou se běžně používat v kusové a malosériové výrobě.
Prediktivní vizualizace výsledků
Budoucností digitálních dvojčat je také jejich využití jako dalšího zdroje dat pro postupy strojového učení a umělé inteligence. „Poslouží jako zdroj dat, která se v procesu výroby buď nedají pořídit, nebo jen obtížně. Do stroje vstupuje řada informací, které umíme posbírat a popsat, ale důležité pro učení algoritmů strojového učení a umělé inteligence je znát také výstupy těchto procesů, zejména z hlediska kvality obrobku, přesnosti, jakosti obrobených ploch. To bez náročného měření obrobku a skenování povrchu nelze obstarat,“ vysvětluje Matěj Sulitka, vedoucí Ústavu výrobních strojů a zařízení a Výzkumného centra pro strojírenskou techniku a technologii (RCMT) Fakulty strojní ČVUT v Praze. Jednou z obrovských příležitostí digitálních dvojčat je právě poskytování prediktivní vizualizace výsledků obrábění a tím i doplnění chybějících vstupů pro strojové učení.
Další otázkou je, jak kontrolovat v průběhu času stav virtuálního modelu v porovnání se skutečnými vlastnostmi stroje. „Vlastnosti stroje se mohou v čase vyvíjet a vlastnosti, na které byl virtuální model nakalibrován, nemusí odpovídat budoucímu stavu stroje za půl roku, za rok,“ naznačuje Matěj Sulitka jednu z otázek, kterými se zabývá v současnosti výzkum.
Odhalit chyby již ve fázi přípravy
Virtuální dvojče má řadu výhod – odhalí chyby dřív, než k nim dojde na stroji při skutečném obrábění, pomáhá optimalizovat výrobní procesy, šetřit náklady, zrychlovat výrobu, věrohodně predikuje výsledky obrábění, ale také pomáhá firmám, aby jejich výroba korespondovala s udržitelností. „Skrývají v sobě příležitost pro optimalizaci procesů obrábění ve vazbě na jejich energetickou náročnost. Umožňují vybrat ty procesy, které budou trvat buď nejkratší dobu, nebo budou vyžadovat nejmenší spotřebu energie,“ nastiňuje Matěj Sulitka, jak lze snížit energetickou náročnost výroby otestováním pomocí modelů spotřeby energie.
Virtuální dvojče významně přispívá ke zkracování časů přípravy výroby. Výrobní stroje nemusí být blokovány přípravnými pracemi, jako jsou testování NC programů, ladění technologických parametrů nebo ladění parametrů CNC řízení stroje. Velké výhody jsou patrné také při vývoji nových obráběcích strojů, kdy virtuální dvojče umožní testovat návrh stroje ve vazbě na jeho předpokládané technologické využití a umožní odstranit chyby, které by jinak vyžadovaly výrobu a testování fyzických prototypů. „Digitální model nám může poskytnout informace o průběhu procesu a jeho výsledcích pomocí detailní vizualizace obrábění a dat, která by bylo obtížné měřit a monitorovat na stroji,“ doplňuje Matěj Sulitka, jak může model i v průběhu výrobního procesu poskytnout plnohodnotnou informaci o tom, co se v procesu děje. „Díky tomu pak lze připravit stroj tak, aby si uměl sám chytře opravit nějaké parametry či řezné podmínky proto, aby se eliminovalo riziko vzniku zmetků nebo nekvalitního výsledku obrábění,“ vysvětluje další výhodu Sulitka.
Využívat se dají například modely vyráběných dílců již v rámci technologické přípravy výroby. S využitím CAM systémů se připraví data pro obrábění a následně se tyto modely používají při měření již reálných, tedy obrobených dílců na 3D měřicích strojích. „Tyto modely se načtou do softwaru měřicího stroje a před samotným měřením se vytvoří programy, díky kterým již pak samotné měření probíhá zcela automaticky,“ popisuje Tomáš Kozlok, vedoucí vývojových projektů a zkušebny ve společnosti TOS Varnsdorf, jak mohou virtuální modely zrychlit a zefektivnit výrobní proces.
Sofistikované modely celých strojů v sobě pak zahrnují nejen geometrický tvar stroje, ale také jeho mechanické a dynamické vlastnosti včetně pohonů, řídicího systému i modelu řezného procesu. „Pomocí těchto modelů pak dokážeme simulovat vlastnosti a chování reálného stroje ještě dříve, než vůbec dojde k jeho výrobě, a predikovat kvalitu a čas vyrobeného dílce včetně vizualizace povrchu a jeho chyby s velmi dobrou shodou vůči reálné výrobě. Díky těmto modelům lze odhalit chyby, které se dají napravit ještě ve fázi přípravy, a ušetřit tak drahocenný čas na stroji a samozřejmě finanční prostředky. Na těchto virtuálních modelech lze kromě simulací provádět i rozsáhlé citlivostní analýzy, které nám umožní z velké množiny možných řešení vybrat optimální, která mají nejzásadnější dopad z pohledu kvality a rychlosti výroby,“ říká Tomáš Kozlok.
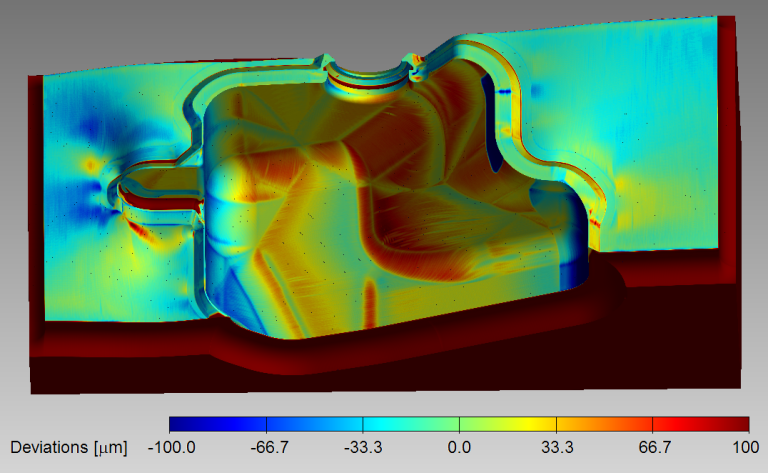
Zkrácení obrábění o hodiny
Virtuální dvojče sestav obráběcích strojů se dá například využívat pro přesný výpočet nosné struktury obráběcího stroje či pohonů stroje. „To nám umožňuje lépe porozumět danému konstrukčnímu uzlu a díky tomu jej dokážeme dobře optimalizovat,“ říká Petr Heinrich, technický ředitel společnosti Kovosvit MAS.
Další možností využití virtuálního prostředí je optimalizace drah nástroje při obrábění, kdy je dosaženo lepšího povrchu a kvality v oblasti přechodů a hran na dílci. „Konkrétně jsme díky této optimalizaci u lopatky plynové turbíny dosáhli časové úspory obrábění více než dvě hodiny. Dále se zlepšila kvalita povrchu a výsledný tvar v oblasti náběžné a odtokové hrany lopatky,“ popisuje výhody Petr Heinrich.
„Využití je velmi široké. My se kupříkladu nyní zabýváme možností optimalizace řezných podmínek, kdy na základě zadání informací o obráběném materiálu a použitém nástroji můžeme s využitím digitálního dvojčete upravit doporučené řezné podmínky od výrobce nástrojů tak, aby byl maximálně využit potenciál obráběcího stroje,“ říká Tomáš Kozlok z TOS Varnsdorf.
Dalším tématem je podle něho využívání klíčových informací o obráběném dílci v průběhu celého výrobního cyklu. Tyto informace jsou součástí virtuálního modelu, který si jednotlivá výrobní nebo měřicí zařízení automaticky načítají a dokážou s nimi pracovat. „Příkladem může být automatické sdílení informací mezi výrobními a měřicími zařízeními. Na základě identifikované odchylky se automaticky vyhodnotí schopnosti daného výrobního zařízení z hlediska kvality výroby a upraví tok výroby tak, aby bylo dosaženo požadované kvality výrobku,“ dodává Tomáš Kozlok.
Stáhněte si přílohu v PDF
Postupná eliminace mezičlánků
Co v současnosti ještě komerčně dostupná řešení digitálních dvojčat v průmyslových aplikacích neumí, je reprezentovat veškeré fyzikální vlastnosti stroje a obrobku. „Tedy včetně poddajnosti struktury stroje, pohonů, regulace pohonů a procesu obrábění, který je zdrojem sil, jež způsobují deformace stroje, nástroje a obrobku a jsou příčinou vibrací. Ty mohou vést až ke vzniku zmetku,“ říká Matěj Sulitka. Právě tato unikátní koncepce modelu digitálního dvojčete stroje a procesu je již několik let předmětem výzkumu na pražském ČVUT. „Velkou předností tohoto modelu je mimo jiné věrohodná vizualizace jakosti obrobeného povrchu se všemi projevy kmitání stroje a nástroje,“ doplňuje Sulitka.
Nejvzdálenějším cílem, ke kterému využití digitálních nástrojů bude směřovat, je podle Matěje Sulitky snaha maximálně eliminovat všechny mezičlánky, které dnes jsou mezi konstruktérem, technologem, strojem a procesem obrábění. „Vizí je, abychom do obráběcího stroje nahráli pouze konstrukční model obrobku a stroj sám si již navrhl způsob, jakým bude dílec obrábět. Aby sám navrhl vhodné parametry obrábění a výstupem potom byl spolehlivý obrobek,“ říká Matěj Sulitka, jak by šlo odstranit v současnosti časově i procesně náročné kroky přípravy výroby. „Můžeme si to přirovnat k 3D tiskárně, do které dnes člověk vloží model dílce a tiskárna jej vytiskne. Tak vypadá vize obráběcího stroje možná vzdálenější budoucnosti,“ zamýšlí se Sulitka.
Článek byl publikován ve speciální příloze HN Strojírenství.
Přidejte si Hospodářské noviny
mezi své oblíbené tituly
na Google zprávách.
Tento článek máteje zdarma. Když si předplatíte HN, budete moci číst všechny naše články nejen na vašem aktuálním připojení. Vaše předplatné brzy skončí. Předplaťte si HN a můžete i nadále číst všechny naše články. Nyní první 2 měsíce jen za 40 Kč.
- Veškerý obsah HN.cz
- Možnost kdykoliv zrušit
- Odemykejte obsah pro přátele
- Ukládejte si články na později
- Všechny články v audioverzi + playlist