Vystudoval střední průmyslovku, obešel se bez manažerského vzdělání a v životě nedočetl jedinou knihu o podnikání. Přesto dnes třiatřicetiletý Jan Skála řídí úspěšnou firmu, která vyrábí díly pro závodní auta všech značek v nejvyšší kategorii mistrovství světa v rallye a od loňského roku i pro formuli 1. „Chtěl jsem závodit a potřeboval si na to vydělat peníze,“ vrací se k počátkům svého podnikání výkonný ředitel firmy RaceX. Od svých čtrnácti let sbíral tituly v rallycrossu, v roce 2010 se stal mistrem ČR na formulových okruzích a o dva roky později se opět v rallycrossu vypracoval ke startu na mistrovství Evropy. K další kariéře mu ale chyběly peníze, a tak se po neúspěšném pokusu o vlastní závodní tým rozhodl založit výrobní firmu na kompozitní díly, která by mu vydělala na návrat na závodní tratě.
Začínal úplně bez prostředků a technického zázemí, první výrobnou byla malá betonová garáž. „Dal jsem se dohromady s Filipem Zavadilem, který v té době studoval kompozity na ČVUT. On tomu rozuměl z technologického pohledu a já jsem měl cit pro byznys,“ vypráví Skála. Kromě citu pro byznys měl také vynalézavost a kuráž, která mu po dvou letech přinesla přelomovou zakázku. „Byl jsem se podívat na mistrovství světa v rallycrossu, kde tehdy startovalo jedno z našich aut. A všiml jsem si, že při nárazech do vozu jiného týmu z jejich auta odpadávají kusy dílů,“ vzpomíná Skála. Prošel si tedy záznam, nafotil v něm kritické situace a obrátil se na závodníky s tím, že má pro ně řešení.
Nabídka přišla ve správnou chvíli. Šlo o tým Kennetha Hansena, který se zrovna v té době stával oficiálním továrním týmem automobilky Peugeot. „Odpověděl mi, že vzal naše vzorky do Paříže, že se jim líbily a že nám budou posílat poptávky. Jenže se vůbec nezeptali, jak jsme velká firma,“ směje se dnes podnikatel při vzpomínce na zakázku, která zdaleka převyšovala jeho tehdejší možnosti. Popisuje to jako nejtěžší tři měsíce svého života, kdy skoro nespal. Z firmy o pěti lidech se během pár týdnů stal dvacetičlenný tým, který se pustil do náročné realizace. Noví pracovníci museli rychle získat dovednosti pro ruční výrobu dílů, pracovalo se ve dne v noci, ale do mistrovství světa v Barceloně se nakonec podařilo téměř celé auto Sébastiena Loeba vybavit díly z malé české továrny. To firmě RaceX otevřelo cestu k dalšímu růstu.
Takhle se vyrábějí rakety
Rozvojem postupně procházela i technologie výroby. Firma vyrábí díly z kompozitních materiálů na bázi uhlíkových, aramidových nebo skleněných vláken. Jejich společnou výhodou je lehkost a každý z nich má pak svá specifika: sklolaminát je levnější, karbon zase pevný, ale křehký, zatímco aramid vyniká svou odolností. Vlákna jsou spletená do tkaniny napuštěné pryskyřicí, z níž se příslušné tvary vyřezávají, vkládají do forem a vytvrzují. „Způsobů, jak vyrobit kompozitní díl, je několik. My jsme začínali na jednodušších technologiích, u kterých není potřeba mít drahé stroje,“ vysvětluje Skála. Nejprve to byla ruční laminace, později vakuová infuze, při níž se pryskyřice nasává do tkaniny pomocí vakua. „Stačí k tomu mít vývěvu za dvacet tisíc korun. Na tom jsme fungovali asi tři roky, než jsme si vydělali na první autokláv,“ pokračuje Skála.
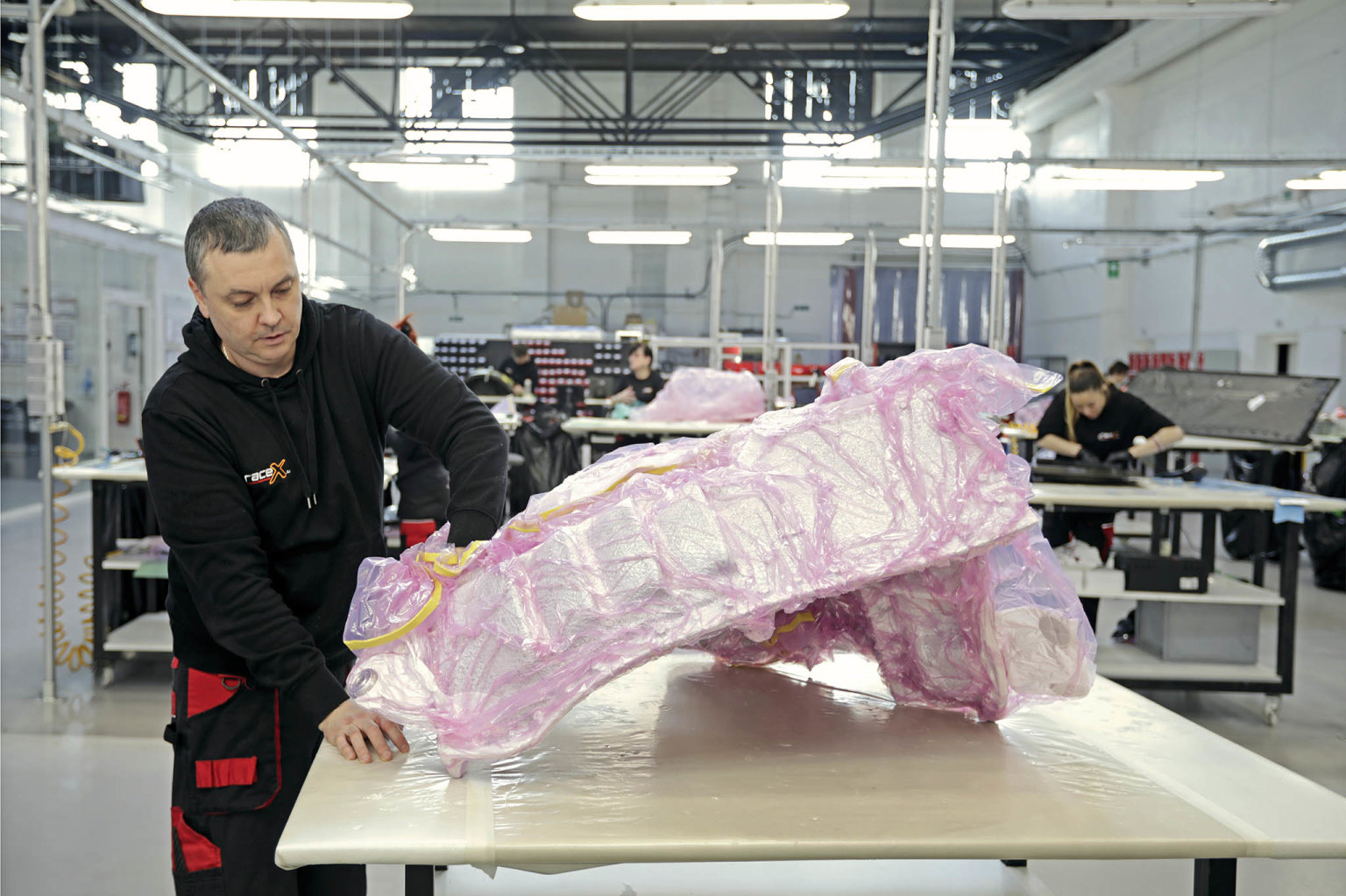
Autoklávy má firma v současné době dva, jsou to velké pece, které vypadají jako ponorky a dokážou uvnitř vytvořit vysoký tlak a teplotu, díky čemuž se kompozitní díly vytvrdí do požadovaného tvaru. „Tohle je v současné době nejpokrokovější způsob, jak díly vyrábět,“ říká Skála a odkazuje na kosmický průmysl, který je jakýmsi průkopníkem technologických novinek. „Než se nová technologie osvědčí v kosmickém průmyslu a zlevní, aby se začala používat pro výrobu letadel nebo později aut, trvá to pár desítek let,“ pokračuje Skála. A protože rakety se dnes stále vyrábějí stejným způsobem jako závodní auta v pražské výrobně RaceX, může si být šéf této firmy jistý, že i v příštích letech zůstane se svými postupy na technologické špičce.
Úspěch své firmy nicméně nepřikládá ani tak technologii, jako spíš souhře schopného týmu, rychlosti a spolehlivosti. V automobilovém průmyslu – stejně jako v každém jiném – rozhodují o úspěchu tři protikladné požadavky zákazníka: rychlost, kvalita a cena. „U každé zakázky se snažíme obstát ve všech třech, ale zpravidla to funguje tak, že když splníte dva z nich, tak tím vyloučíte ten třetí,“ hodnotí situaci své firmy mladý podnikatel. Za svou konkurenční výhodu považoval zpočátku především rychlost, malá firma se mohla nečekaným zakázkám pružně přizpůsobit. Dnes pracuje v RaceX 70 zaměstnanců a společnost pomalu narůstá do korporátních rozměrů, kde je pro Skálu a jeho nejbližší kolegy výzvou vyladit procesy tak, aby si firma i v této velikosti zachovala svou efektivitu.
RaceX
Firmu založil před deseti lety automobilový závodník Jan Skála spolu se strojním inženýrem Filipem Zavadilem.
Specializuje se na malosériovou výrobu karbonových komponentů pro motorsport, díly dodává do závodních aut od mistrovství světa v rallye (WRC) přes prestižní okruhové závody až po formuli 1.
Firma sídlí a vyrábí v Praze, v současné době má 70 zaměstnanců.
Letos byl Skála nominován do soutěže o titul EY Podnikatel roku České republiky 2024.
Firma bez papírů
Robotizované linky v továrně RaceX v pražských Komořanech nenajdete. Práce na přípravě jednotlivých dílů vyžaduje pečlivost lidských rukou, kterou zatím podle ředitele automatizovat nejde. V prostorné výrobní hale tu u pracovních stolů postává pár desítek zaměstnanců, kteří ručně separují formy, řežou na plotru impregnovanou tkaninu do přesně vyměřených tvarů, ty pak vkládají do forem a pečlivě balí do růžových vakuových pytlů, aby je připravili na vytvrzení v autoklávu. Ručně pak také ořezávají a zabrušují hotové díly, než je odevzdají ke kontrole a odešlou zákazníkům.
U každého pracovního místa nechybí tablet. Celý proces výroby je totiž digitalizovaný do posledního detailu, každý díl má svůj QR kód s kompletními daty o jeho vzniku a každý pracovník má přesně stanovené postupy v personalizované digitální aplikaci. Po dokončení jednotlivého kroku odklikne zaměstnanec na tabletu, že je splněno, a zobrazí si další úkol.
„Dnes už ve firmě nemáme prakticky žádné papíry. Pracovník, který u nás nastoupí, dostane tablet a přihlásí se do aplikace, kde má kompletní instrukce ke své práci krok za krokem,“ představuje Skála digitalizovaný systém, který od něj občas na odborných konferencích okukují podnikatelé z mnohem větších firem.
Na každou pracovní úlohu má zaměstnanec stanovenou časovou normu a ta se průběžně upravuje podle jeho výkonnosti. Na tabletu si může průběžně kontrolovat, kolik času mu ještě na daný úkol zbývá, nebo zjistit, jaké ho čekají další kroky i plán na příští den. „Umožňuje nám to pružně upravovat proces výroby. Když dojde k nějaké změně, což se dost často stává, informace se v systému propíšou všem, takže nemusíme pobíhat po firmě s papírovými průvodkami a dohledávat, která verze je aktuální,“ uvádí jako jednu z výhod digitalizace Skála. Důležitá je i sledovatelnost každého jednotlivého dílu. Když se objeví závada, je snadné zjistit, ve které fázi výroby došlo k chybě a kdo je za ni zodpovědný.
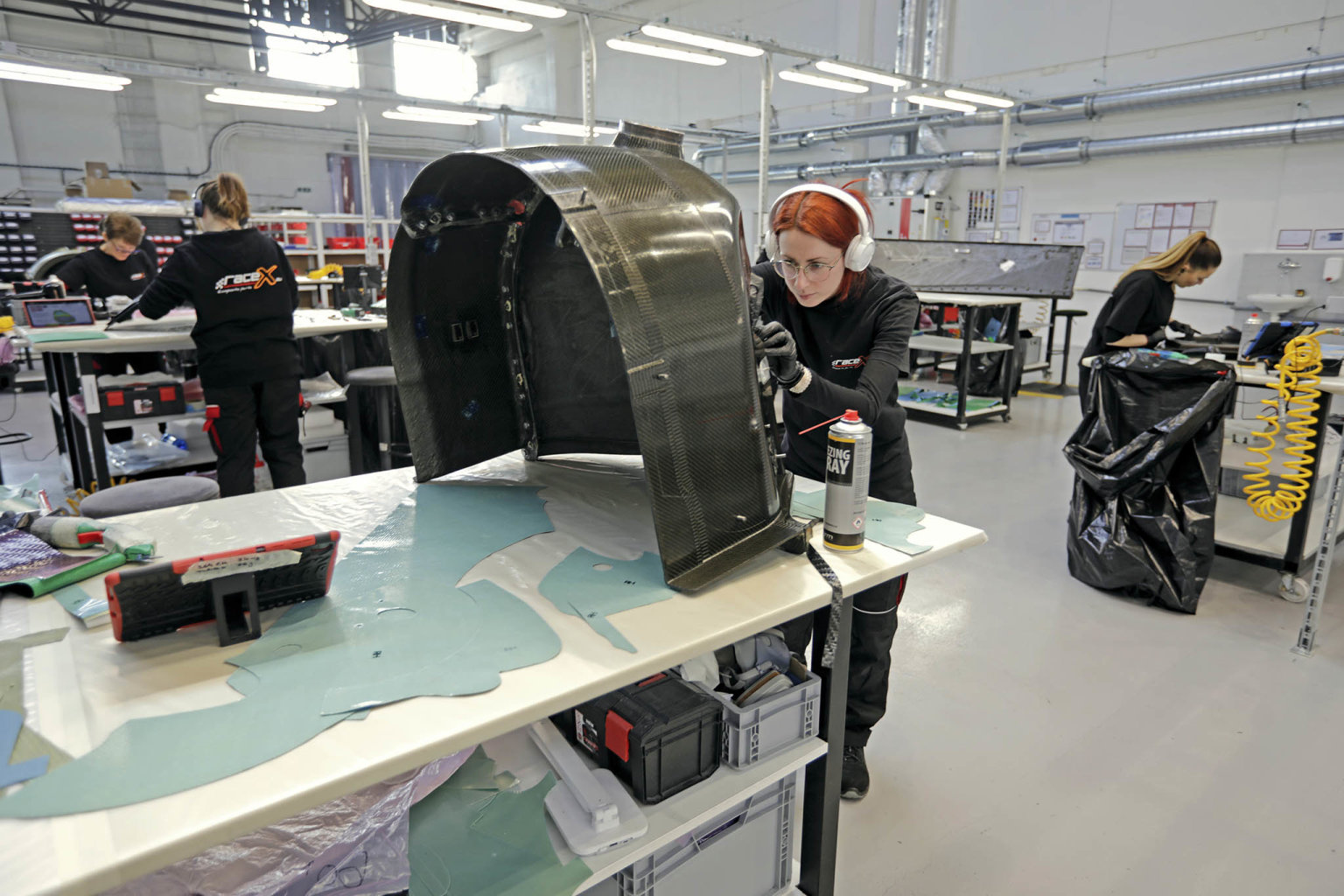
„Samozřejmě uvažujeme o tom, že do systému zapojíme i umělou inteligenci, protože máme velké množství dat, která ještě můžeme v budoucnu využít lépe,“ těší se Skála. Nápady na další inovace nehledá u konkurence, ale ve vlastní hlavě a u kolegů. „Chodím po výrobě, bavím se s lidmi a přemýšlím, jak to dělat co nejlíp. Kdybych kopíroval jiné firmy, zůstanu vždycky jen v jejich stínu a nikdy je nepředběhnu,“ popisuje svůj přístup, ve kterém nezapře mentalitu závodníka.
Zaměření na výkon a efektivitu je znát i z jeho personální politiky. Při náboru nových zaměstnanců neklade důraz na technickou kvalifikaci lidí, ale jde mu o loajalitu a chuť se zlepšovat. „Náš obor je tak specifický, že se to stejně každý naučí až tady,“ říká. Ještě před odesláním životopisu si uchazeč může pomocí elektronické kalkulačky na webu firmy spočítat, kolik si při nástupu vydělá, o kolik se jeho mzda může zvýšit díky odměnám a jak rychle bude v čase růst. Nástupní mzda je tu nižší, ale po určité době začne rychle růst. Firma se tím chce vyhnout náročnému zaučování kolegů, kteří by nastoupili jen kvůli penězům a po krátké době podnik opustili. „Nejsem zastáncem vysoké základní mzdy. Chci platit lidi za to, že jsou šikovní a pracovití, ne za to, že chodí do práce,“ objasňuje Skála.
Nastavil proto v týmu systém provizí, ve kterém se firma s každým pracovníkem částečně dělí o svůj zisk. „Z každého prodaného dílu dostanou malý podíl ti, kdo na něm pracovali,“ vysvětluje ředitel. Provize, prémie i placené přesčasy najdou zaměstnanci ve firemní aplikaci, včetně známek, které jim za kvalitu každého jednotlivého výrobku uděluje jejich nadřízený. Kdo je šikovný, může si podle Skály přilepšit na těchto složkách o více než třetinu své měsíční mzdy.
Nejvyšší meta dosažena
Sen mladého závodníka, že se díky podnikání naplno vrátí ke svému oblíbenému sportu, se ale pod tíhou byznysu trochu rozplývá. „Závodit můžu do čtyřiceti let. Brzy mi bude čtyřiatřicet, takže mám na to ještě asi šest let.“ Jenže k tomu, aby mu firma zaplatila mezinárodní šampionát, ji musí vybudovat do určité velikosti a to teď znamená investovat do jejího rozvoje. „Momentálně jdou všechny prostředky do firmy a na závodění moc nezbývají peníze ani čas,“ popisuje začarovaný kruh, ve kterém se ocitl.
Stáhněte si přílohu v PDF
Jeho společnost mezitím dosáhla nejvyšší mety, jakou si v oboru lze představit, a od loňského roku dodává díly i pro formuli 1. „Zatím děláme jen menší zakázky, ale příští měsíc přiletí partneři na audit a pak bychom pro ně mohli začít vyrábět i velké díly,“ prozrazuje Skála. Technologicky to podle něj nepředstavuje velké změny, klade to ale větší nároky na kvalitu výrobních procesů. „U formule 1 se musí ještě důkladněji hlídat dohledatelnost každého dílu, včetně informací o tom, ze které konkrétní role tkaniny byl vyroben,“ dodává.
V nejbližších letech bude navíc muset najít pro firmu nové prostory. „Chtěl bych se vyhnout logistickým parkům, raději bych oslovil nějakou vesnici v koridoru kolem Prahy, pro kterou by naše přítomnost mohla být atraktivní a oboustranně výhodná,“ odhaluje své plány.
Zároveň pracuje na rozšíření výroby do dalších odvětví. Výhodou kompozitů je, že mají široké využití. Kromě motorsportu se používají i v letectví, v kosmonautice, v obranném nebo lodním průmyslu a při výrobě sportovních nebo zdravotnických pomůcek. Už teď firma RaceX zajišťuje menší dodávky do automobilového a zbrojního průmyslu. „Hledáme nové příležitosti, protože potenciál toho materiálu je obrovský,“ uzavírá podnikatel.
Článek byl publikován ve speciální příloze HN Budoucnost strojírenství.
Přidejte si Hospodářské noviny
mezi své oblíbené tituly
na Google zprávách.
Tento článek máteje zdarma. Když si předplatíte HN, budete moci číst všechny naše články nejen na vašem aktuálním připojení. Vaše předplatné brzy skončí. Předplaťte si HN a můžete i nadále číst všechny naše články. Nyní první 2 měsíce jen za 40 Kč.
- Veškerý obsah HN.cz
- Možnost kdykoliv zrušit
- Odemykejte obsah pro přátele
- Ukládejte si články na později
- Všechny články v audioverzi + playlist